THREE
TRING
INDUSTRIES:
Canvas Weaving, Brickmaking, Metalworking
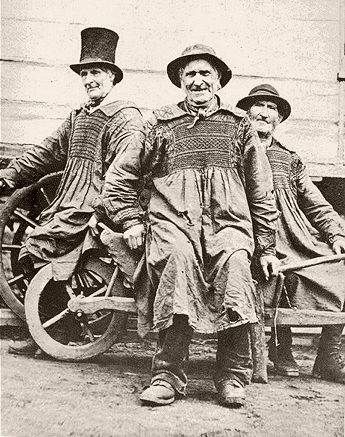
Brick makers
Wendy Austin
――――♦――――
CONTENTS
――――♦――――
FOREWORD
In the Victorian period, most towns, and even villages, were
self-sufficient in that local businesses and shops provided for
nearly all of the inhabitants’ day-to-day needs. Tring was no
exception, and nobody had to travel far to find both employment and
commodities.
Apart from the activities at Tring silk mill, which was an unusually
large concern to find in a small market town, various other
industries sprang up, some of course related to transport
necessities in the age of the horse. These small businesses
were founded and run by craftsmen, and often passed down through the
generations, although some of the stories ended sadly due to
bankruptcy or forced closure.
The subject of the silk trade in the town has been covered in a
separate book,
Tring Silk Mill (published 2008,
reprinted 2014). The essential industry of flour milling has
also been written up in
Gone with the Wind: Windmills and those around
Tring (published 2010). This present booklet covers
three other industries trading from the late 18th century and, to a
certain extent, to the present day. Canvas weaving has now
disappeared completely from the local scene but ironworking, forging
and one firm of brickmakers still carry on in the locality.
It has been difficult to establish the exact dates and persons
involved in some of the old industrial concerns, especially
brickmaking. But the content is as accurate as can be
discovered at the time of writing; if any reader knows more details
of these professions in Tring, I should be pleased to know.
References to source material are acknowledged in the main text or
footnotes, but my thanks for information and loan of pictures also
goes to Michael Bass, Shirley Bloomfield, Harvey Burch, Jill Fowler,
Julie and Gilbert Grace, staff of Hammer & Tongs, Jimmy Honour, John
Horn, Bert Hosier, Mick Jones of BBONT, the late Ron Kitchener, Jon
and Debbie Lovelace, staff of Matthews Brickworks, Rebecca
McCloskey, David Metcalfe, Stuart Pearce, Ann Reed, David Ridgwell,
Paddy Thomas, Elizabeth Tory, and especially to Ian Petticrew who
has formatted and edited this book.
W.M.A.
December 2017
――――♦――――
1. EARLY INDUSTRY IN TRING
From the time of its first Market Charter in 1315 and before, Tring
has always been a small agricultural market town, but in the 19th
century some successful industry was established, helped in measure
by the coming of the
Grand Junction Canal and later, to
a greater extent, by the
London & Birmingham Railway.
In 1823 a successful cotton and silk manufacturer, William Kay
(1777-1838), purchased the Tring Park estate but not with the
objective of living in the mansion house, for he preferred to remain
in London minding his other investments. He claimed to have
spent £30,000 erecting and equipping a five-storey silk throwing [1]
mill in Brook Street which processed imported skeins from China and
Bengal ready for despatch to various silk weaving mills, both
locally and in Macclesfield and Coventry. This undertaking was
powered by a huge 22ft.-diameter waterwheel driven by the diversion
of various streams which ran underground beneath Tring; later this
was supplemented by steam.
At its peak the mill employed as many as 600 people, including a
large number of children (some as young as eight years old) sent
from both local workhouses and those in St Margaret’s and St
George’s parishes in London. The children were housed in a
long dormitory building fronting the mill, provided with work
clothes, and reasonably well fed. All hands worked very long
hours, although the children were supposed to receive some
rudimentary education, and conditions may not have been so harsh for
them as those in mills in the north of the country.
In 1872 the first Lord Rothschild (1840-1915) acquired the Tring
Park estate of which the mill was part; by then, the silk trade
generally was already in serious decline due mainly to cheaper
foreign imports. Not wishing to cause hardship, he continued
to let the business run at a loss until the doors were finally
closed in 1898. The top two storeys and tall chimney were then
removed, but the remainder of the original premises – somewhat
altered – can still be seen in Brook Street and now serve to house a
variety of industrial units.
Very much smaller concerns were the canvas weaving shops which
sprang up in various parts of the town; looms were also set up in
the Parish workhouse. These workshops produced all types of
canvas from that used on embroidery frames to coarse quality for
horses’ nosebags. The largest premises were in Park Road, and
others were established in Akeman Street,
Dunsley,
off Langdon Street, and later, Charles Street, the latter not
closing until the 1920s. Again, some local child labour was
used, usually boys referred to as ‘half-timers’, meaning they
attended school for part of the day either before or after working
in the factory.
From the medieval period onwards various types of metalworking was
carried on in Tring. When all transport was horse-drawn, local
smithies were a necessity, and as agriculture became more
mechanised, blacksmiths could be found in even the smallest towns.
Some businesses combined forges at the rear of a shop which sold all
sorts of hardware, some made on the premises. Examples of work
produced by these firms can still be seen around Tring.
One industry in the town that still operates today is milling –
Heygates at
New Mill being the last working flour mill in Dacorum.
At Gamnel a windmill had been built on a strategic site alongside
the canal, joined later by a brick-built six-storey mill erected
under the ownership of the Mead family at the time when steam was
replacing wind power (the windmill finally being demolished in
1911). The adjacent wharf was then a busy place as the trade
included dealing in hay, straw, gravel, coal, coke and general
carrying by water. Part of the complex included a
boat-building business run and later owned by the Bushell Brothers,
a concern that Thomas Mead had established to maintain his own fleet
of narrow boats. Part of the original mill building remains,
but its interior has long been transformed. The mechanical
shafts, cogs, belts and sets of grindstones it once housed have been
replaced by pipe-work that connects the grain silos with rows of
cabinets housing the computer controlled steel milling rollers.
Over the years many other small industrial concerns served local
needs, including several breweries, a tannery, a carriage builder, a
lime works, and a mineral water factory. Brief mention should
also be made of the two cottage industries of Tring, straw plaiting
and, to a lesser degree, lace making. Essential to the local
economy in the 19th century, this work could be carried out at home,
mainly by women but also by children. Without it many would
have gone hungry for it helped to keep the wolf from the door,
especially during times of agricultural depression when there was
little employment for the menfolk.
However, just over one hundred years ago a report in The Bucks
Herald lamented:
“. . . . by late Berkhamsted has become predominant. Tring
formerly was as an important town as Watford then was and, perhaps
excepting Hemel Hempstead, its market was the largest in West
Hertfordshire. With a flourishing silk mill, employing a large
number of people, several canvas-weaving works doing good business,
and the plait industry in and all around the district, Tring was a
thriving place and a large measure of enterprise and endeavour
obtained. But during the last generation all these industries
have almost died out and the population declined in all the villages
around Tring. Tring has necessarily had to take a backward
place by reason of its insular
position and its distance from the railway . . . . ”
Sic transit gloria
CHAPTER
NOTES
1.
Silk throwing is the industrial process wherein silk that has been
reeled into skeins, is cleaned, receives a twist and is wound onto
bobbins. The yarn is now twisted together with threads, in a
process known as doubling. Colloquially silk throwing can be
used to refer to the whole process: reeling, throwing and doubling.
Silk had to be thrown to make it strong enough to be used as the
warp in a loom.
――――♦――――
2.
CANVAS WEAVING
Canvas, a durable plain-woven cloth, was traditionally made from
hemp (cannabis sativa) an undemanding plant with a long fibrous stem
and six times as strong as cotton. The fibres, from 3ft. to
15ft. in length, commonly called bast, grow on the outside of the
woody interior of the plant’s stalk, and under the outermost part of
the bark.
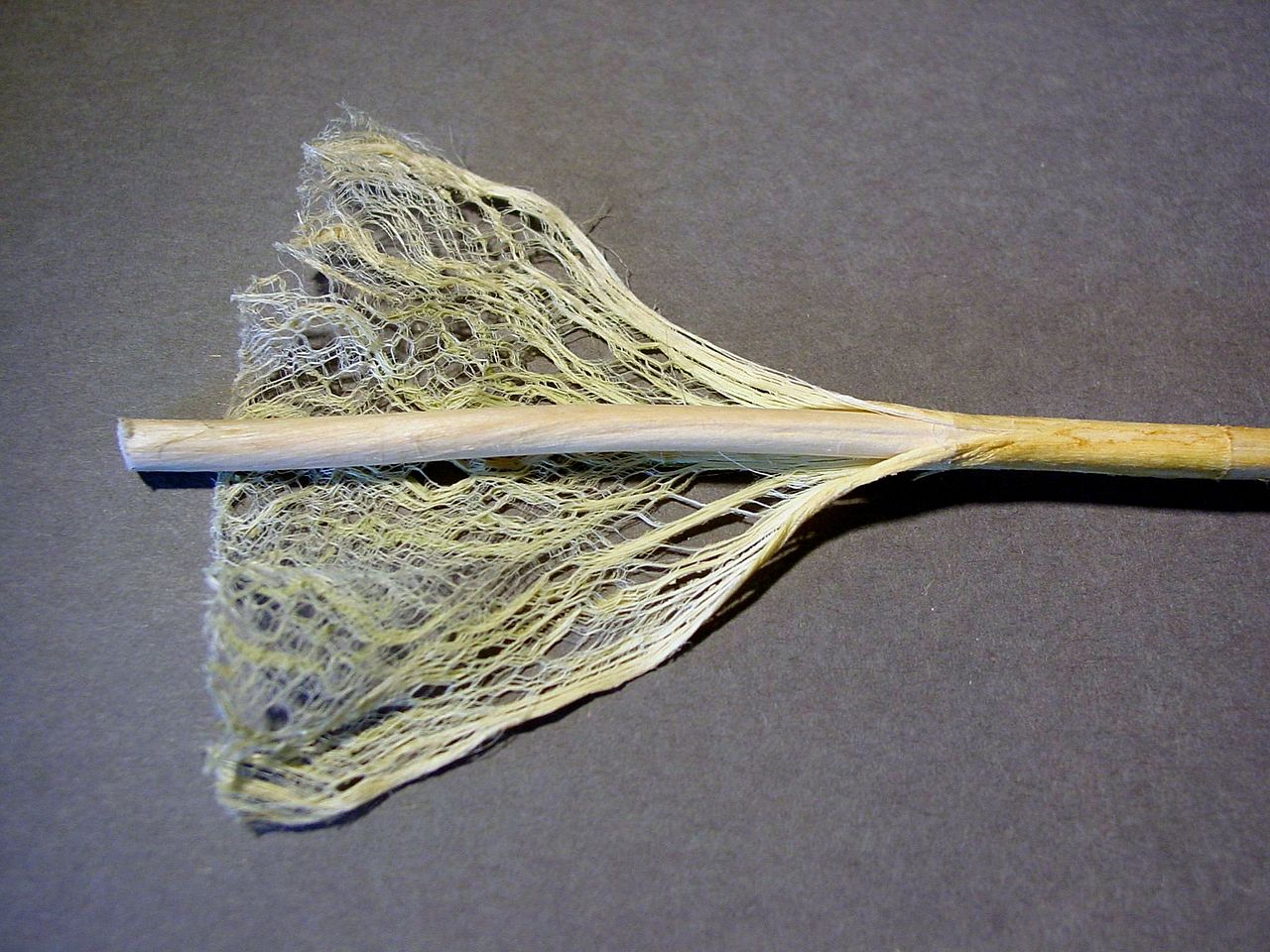
Stem of the hemp plant
(Cannabis Sativa)
There does not appear to be a tradition of hemp growing in the Tring
area (although there is a local ‘Hemp Lane’ which winds up from the
main road to Wigginton village), and no one can say exactly why
canvas weaving started as a small industry in various locations in
the town.
Tring local historian Arthur Macdonald writing in the 1890s states:
“The canvas industry is said to have been introduced [to
Tring] by a colony of Flemings who settled here. Some of
their names remain, as Delderfield or Delderfeldt (‘Darofel’), and
Wilkins (‘Wilquin’)”. These people who migrated to England
following persecution of their Calvinist faith on the Continent
brought with them many craft skills, and were often master weavers
or journeymen specializing in various branches of the textile
industry, mainly silk, although some Huguenots had practiced the
craft of canvas sail making in England since long before then.
No firm records can be discovered of these descendants of exiles
actually arriving in Tring, but certainly a number were connected
with Hemel Hempstead, where the Fourdrinier brothers installed a
French-designed machine for the paper-making industry in that
locality and where, it is said, the colony had its own cemetery. [1]
The first documented evidence of canvas weaving in Tring comes from
entries in the Militia Lists [2]
from the middle to the end of the 18th century, and these record men
working as rope-makers, as well as one flax man and one hemp
dresser. [3]
By 1772, names of members of Tring families engaged in canvas
weaving appear, including one Cutler, two Catos and several Olneys.
Mention is made in a legal document of 1815 relating to lands held
by the Tring Park Estate where the name Jackson Harding and several
other weavers are shown as well as a ‘weaving shop’, and it is
possible that this refers to a premises engaged in canvas weaving.
(One of the Olneys – see below –had the given name of ‘Harding’,
implying descent or connection with Jackson Harding.)
Pigot’s Directory from 1825 to 1839 lists four proprietors of
weaving shops, and Arthur Macdonald describes these as follows:
“Entering the town from the east, the first building on the left
is the pretty pair of cottages [Dunsley Cottages] built by
Lord Rothschild on the site of an old canvas weaving shop, then
owned and occupied by Mr John Burgess, and before him by Daniel and
Harding Olney. The Olneys were a family of some position in
the town, being the principal canvas manufacturers and possessing
several properties. William Olney had weaving shops in Akeman
St., which he converted into the Akeman Brewery. [4]
The present brewery in Frogmore St. was first a canvas factory
worked by one Cutler. William Cato commenced canvas making at
The Oak in Akeman Street, and subsequently built the factory in Park
Road which is now the only relic of the trade.”
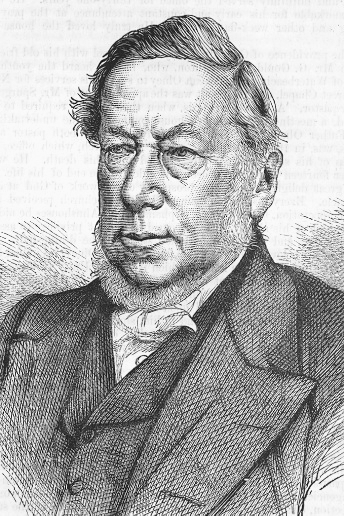 |
Thomas
Olney (b. 1790) |
By ‘some position
in the town’ Arthur Macdonald presumably refers to the Olney
family’s high standing at the New Mill Baptist chapel, at a time
when Non-Conformity was at its height. Daniel Olney senior was
Deacon at that church, and his brother, Thomas, who had been sent by
their father to London to trade as a wholesale mercer went on to
become one of the Reverend Spurgeon’s [5]
right-hand men.
All qualities of canvas were woven in the various workshops, from
heavy-duty for sacking, lighter weight for work smocks, down to very
fine products for use on embroidery frames and for curtain lining.
The smock shown below is worn by Tring labourer James Stevens, these
garments being the traditional wear of men and boys engaged in farm
work, and often embroidered with emblems showing their particular
trade, thus enabling them to be readily identified at the annual
hiring fairs. [6]
John Burgess, advertising his trade as “canvas manufacturer of
open canvas for ladies needlework, gunpowder canvas, cheese cloths
etc.” carried on weaving in the premises at Dunsley until it was
shut down in 1883 [7]
and demolished some years later, along with other nearby properties,
to make way for the erection of Dunsley Cottages opposite the Robin
Hood pub.
The following extract of 1840 taken from Osborne’s Guide to the
London & Birmingham Railway, gives some description of the
procedures at the largest of the canvas workshops operating at that
date:
“Tring claims to have commenced the canvas trade before any other
town in England. There are four manufactories, in which
upwards of a hundred persons are employed. The yarn is brought
from Yorkshire, and wove by hand-looms; the first process is
performed by boys; it consists in winding the yarn from the hand
upon the spools, these are then taken to the warping mill to be
wound into large warps ready for the loom; it is then taken to the
loom and woven by men. The work is not considered very hard
and the time of daily labour is from ten to twelve hours; the men
get about 16s. per week, the boys about 3s. Mr Cutler, the
largest manufacturer in the town, works 20 looms and employs 40
persons.”
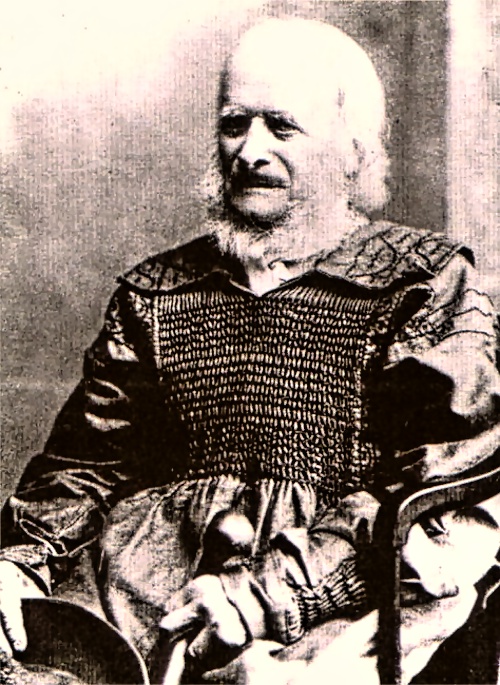 |
James
Stevens (1808-1911) |
In addition to
his canvas weaving business, George Cutler also bought a small silk
throwing mill in Frogmore Street, Tring, a venture that had not
flourished under the previous ownership of William Shipley, when a
notice of ‘Sale under Distress of Rent’ appeared in the Bucks
Herald in 1858. Three years later Cutler also shut up shop
and sold the premises and all assets.
As mentioned by Arthur Macdonald, William Cato moved his weaving
shop from Akeman Street to Park Road, where Thomas Cato is listed in
the 1851 census as employing 11 men, and in Kelly’s Directory
of 1869 as “manufacturer of open canvas for Berlin work, [i.e.
large-stitch wool embroidery], and gunpowder canvas.”
The census returns for Tring show all those engaged in the canvas
weaving trade, including the ‘quill winders’ who were lads known as
‘half-timers’, since they were obliged to attend school for a half a
day in either the morning or afternoon. The rate then was
half-a-crown for half a day which was not considered a good wage,
resulting in a constant change of boy workers. The following
photographs show the Park Road weaving shop as it was around the
turn of the century.
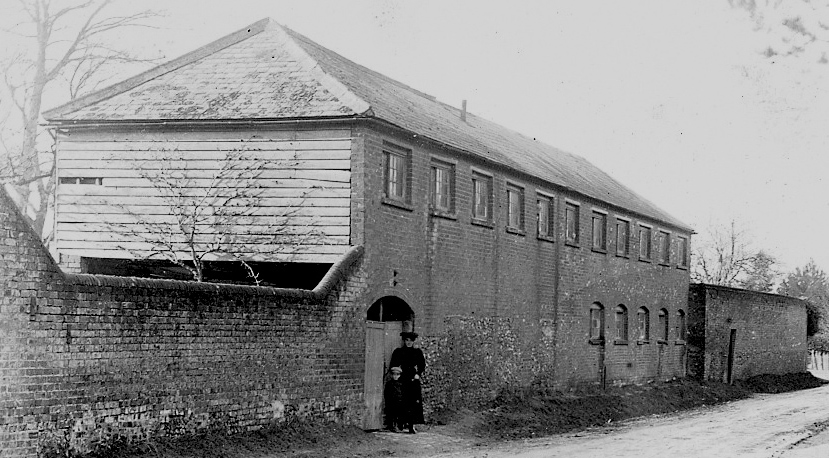
Cato’s weaving shop in Park Road, exterior and
interior.
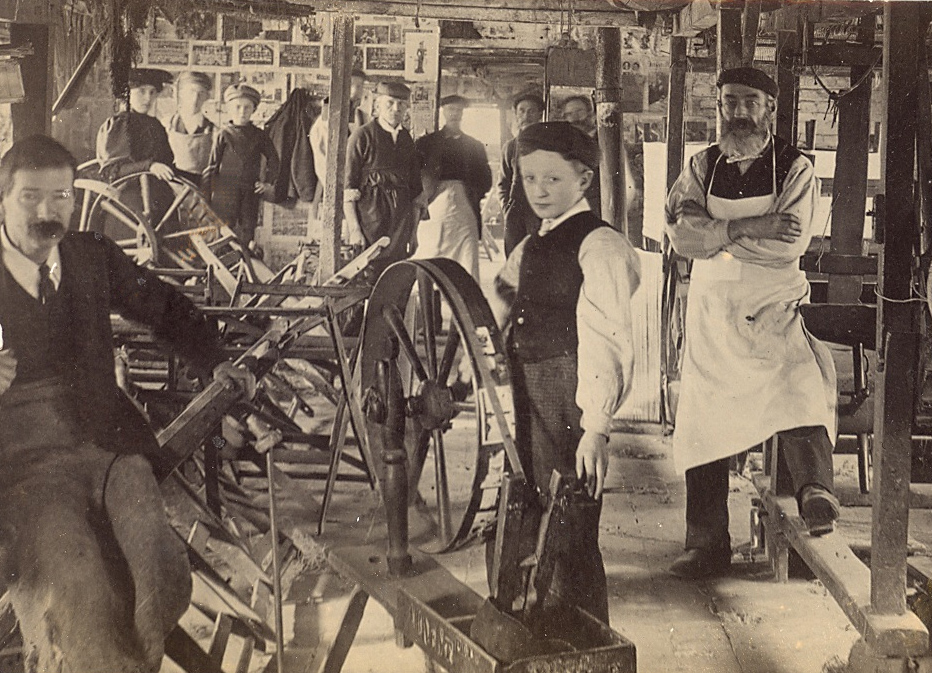
It appears that the men from the workshops were reasonably good at
cricket, as an account of 12th August 1871 in the Bucks Herald
informs that a match played on the Bowling Green [8]
between Tring United Club and the Canvas Weavers resulted in a win
for the latter.
Most towns of any size had at least one rope maker, and listings for
Tring in a trade directory of 1839 show four Rope and Twine Makers,
all working in Market Street (now called the High Street). In
1851 John King, described as a Master Rope Maker, is plying his
craft of rope and twine spinning in his premises in Park Road where
he remained until approximately the early 1890s. It was
perhaps no coincidence that his house and workshop were almost
immediately opposite to Cato’s canvas weaving shop, as both trades
would have required similar materials.
The latter was taken over by George Cato, but at the time of his
death in 1906 the business was in sad decline. Thirty years
before this, in reports of political meetings in the town, the
Conservative Party had bemoaned the fact that the number of Tring
workers in both the silk and canvas factories had dramatically
reduced: “Not many years ago there used to be something like 60
canvas weavers in the town, and now there were 16. Would they
know the reason? It was Free Trade. The Frenchman made
the canvas and it was admitted here duty free, so that the
Englishman could not compete with him.” This laid the
blame firmly on French imports endorsed by the Free Trade policies
advocated by the Liberal Party.
George Cato’s obituary in the Bucks Herald in 1906 outlined
other causes and also lamented that
“. . . . in recent years [the industry] has fallen upon
evil times, the old method of weaving having been superseded by more
rapid and economical processes. The old weaving shop in Park
Road has played its part in the industrial history of Tring, and
there are men employed there now who have spent the whole of their
working life – in some cases more than 40 years – in the shop.
To them and to others the future of the business is a matter of
grave anxiety.”
It may be that a few of them found employment in the fifth and last
canvas weaving premises to be operational in Tring. Named
Gravelly Furlong, sited at the rear of No.12 Charles Street, it is
shown in Kelly’s Directory of 1855, and was also owned by a
Cato (James), and later taken over by Charles Cato. He
produced beautifully fine, soft canvas especially used for the
lining of curtains, the merit of which was recognised in 1886 at a
large Industrial Exhibition held in Berkhamsted when Charles Cato
was awarded a medal. Hearsay, although this cannot be
verified, states that the shop also wove high quality cloth for army
uniforms. Several prestigious department stores were
customers.
In February 1907, when the workforce went for dinner, a disastrous
fire broke out in the drying room near to a stove; a length of
canvas, part of a large order for Whiteleys of London, ignited.
Cato attempted to put out the blaze but within a few minutes the
building was enveloped in flames. Fortunately the Fire Brigade
prevented the fire spreading to adjacent houses, but they were
unable to save the workshops. The damage was estimated at
around £800 but this was covered by insurance, and five months later
plans for a new weaving shop had been passed by the Council and a
rebuild was soon underway. After the death of Charles Cato,
the business was carried on by his son who had spent his working
life with his father until ill health eventually forced his
retirement.
This last remnant of the industry eventually went the way of the
others, when it finally closed down following the death of Frederick
Cato shortly before WWII. The premises then became a ladies’
clothing factory, specialising mainly in sewing coats. Known
as B. H. Baker & Son and owned by Barnet and Annie Baker, the firm
employed both males and females, and in the 1950s frequent
advertisements appeared in the Bucks Herald offering “the
opportunities for young people to learn a useful trade in tailoring,
machining, finishing and pressing.”
Arthur Baker conveyed the property to Kenneth Pegg [9]
in 1977 and an application was submitted for change of use from
industrial premises to conversion to two private dwellings.
Pegg extensively remodelled the building, using various interesting
items of architectural salvage. Now approached by a drive
leading off the upper part of Albert Street, and after several
changes of ownership, the property has been converted to form one
large house.
Chapter Notes
1. From article in The Gazette, 12 May 2007.
2. From 1757, lists of men from various parishes with liability to
serve in the military if called upon. Their ages, occupations
and any disabilities were shown.
3. A worker who separated the coarse part of the hemp with a toothed
instrument called a hackle. Once smooth, the hemp could be
spun.
4. From Bucks Herald 12 February 1859: For Sale by Mr. W.
Brown by directions from the Trustees of the late Miss Sarah Olney “A
Brewery and a Canvas Weaving Shop of six floors, drying house,
stabling and other convenient buildings ……….”
5. One of the leading Non-Conformist churchmen of the era.
6. Hiring fairs, also called statute or mop fairs, were regular
events in pre-modern Great Britain and Ireland where labourers were
hired for fixed terms.
7. Account from the Bucks Herald.
8. An area of meadow behind Brown’s Maltings in Akeman Street.
9. Kenneth Pegg was convicted, tried and sentenced to a 26-year term
for murder in 1985.
――――♦――――
3. BRICKMAKING IN THE CHILTERNS
Overview
The first stage in brickmaking is to obtain a supply of suitable
clay. That used for brickmaking required several properties;
it had to be plastic when mixed with water, have enough tensile
strength to keep its shape, and its particles must fuse together.
The deposits of brickmaking clay around Tring were insufficient to
support large commercial businesses, but sufficient to enable local
brickyards to manufacture on a small scale. These brickyards
also provided welcome employment in a largely agricultural area
where work at times was spasmodic due to weather conditions and the
slumps in agriculture caused by cheap imported foodstuffs, such as
American and Canadian grain and, later, frozen meat.
Clay was traditionally dug in the winter months to allow it to be
broken down by frost. It was then wetted and mixed with a
loam-like substance such as sawdust or wood chippings. An
account by Bert Hosier, born 1928, [1] gives a
good description of the site at Outwood Kiln, Aldbury, (Chapter
4) during the
time of his childhood. With his permission, an extract is set
out below:
“. . . . I well remember the brickyard in full working order, the
deep clay pits where all winter the men toiled digging out the clay,
filling the large round wooden buckets which were hauled up by hand
windlass. One man had a slight hump on his shoulder, and I
used to wonder if he had been hit by a bucket. A light railway
track with side-tipping trucks took the clay to the working area,
the only braking system being a length of cordwood forced against
the iron wheels. Gradually a large mound of clay rose up near
the brickmaking shed, ready for better weather to arrive.
In due course the clay was ‘soaked down’, i.e. pulled from the mound
with long handled hoe-like implements, then well watered and tipped
into the pugmill. [2] This was a
hole in the ground housing grinding blades turned by the constant
perambulations of a horse attached to a wooden arm. The pug
was barrowed to the making tables where four men actually made the
bricks, slapping an accurately guessed amount of clay into the
sanded iron mould, any surplus being taken off with a wooden
striker. The fresh bricks were turned out and placed on to the
special iron-wheeled flat barrow to be wheeled out to the ‘hacks’
(i.e. frames for drying bricks before firing) and they would then
dry in the sun.
Stacked in an openwork formation and with hack covers always at hand
in case of rain or frost, they remained in the open until ready for
burning. During this time they would be ‘skintled’ (i.e.
turned) to present a new face to the sun and air. When safe to
handle, the bricks were stacked in the open topped kilns where
firing and temperatures, learned by experience over many years,
turned the clay into the multi-coloured reds and greys of the facing
bricks for which the yard was renowned.
The
grade of clay needed eventually ran out, so the fence would ‘fall
down’ and be replaced a few yards back to gain more ground and clay.”
Another child resident of Outwood Kiln cottages was Mary Janes
(d.1978) whose father was one of five brick-makers working at the
site. She has left a few recorded memories of how things
were then:
“. . . . The bricks were made in wooden moulds, the base of which
was screwed to the table and the sides came off. These moulds
were dusted with sawdust, the clay was beaten in hard, the excess
scraped off, and the bricks were laid in long barrows to be stacked
and dried in the sun. There was no piped water, the supply
coming from a tapped spring feeding the horse pond at the back of
the cottages. It was a very busy yard which turned out facing
bricks of best greys, multis and reds (which had not been baked hard
enough).”
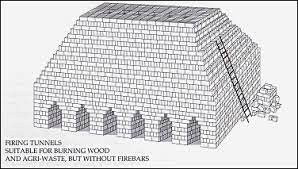
Above: clamp Below:
Scotch kiln
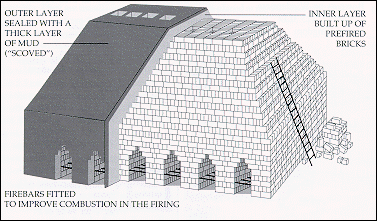
When dry
the bricks were then fired, for which the use of ‘clamps’ was the
oldest and most rudimentary method. In its basic form a clamp
is a carefully constructed stack of unfired (or ‘green’) bricks,
such as that pictured above. However, most brickyards used
some form of permanent kiln, such as the ‘Scotch kiln’. This
was a clamp enclosed within four permanent walls with fire holes in
the sides that led under a perforated floor onto which the bricks
were carefully stacked.
Firewood and coal were the most common fuel sources used for firing
bricks. The heat from the fire passed up through the bricks
and out of the top of the kiln. Smaller brickyards generally
had single fire kilns into which the bricks were loaded, the kiln
lit, and the bricks burnt. The kiln had then to be allowed to
cool before the bricks could be removed, the process taking about a
week to complete.
In addition to using local clay, Tring brick-makers also obtained
supplies of clay and sand from other areas, from which they moulded
the ‘multi-coloured’ bricks featured in some of their
advertisements. Basically, iron chemicals produce red clay;
magnesium produces cream; and carbon produces various shades of
grey, blue and black. As with pottery making, glazed bricks
are obtained by adding salt to the kiln.
As with other labouring occupations of those times, the work of the
brickmaker was hard and the hours long. Until 1871 child
labour was used extensively in large brickworks, and census returns
show that boys were employed in some of the brickyards in the Tring
area. [3]
Other uses of local clay and flint
The flints-with-clay found in the area of the Chiltern Hills around
the Hertfordshire/Buckinghamshire border yielded much valuable
material that could be put to a number of uses. Old maps of
the Victorian period are dotted with pits of different types, marked
as clay, chalk or gravel.
A practice known as ‘clay clapping’ (aka ‘puddling’) was carried out
in some local hilltop villages such as Cholesbury and Buckland,
whereby clay was dug and then used to line ponds, ensuring retention
of water for both agricultural and domestic use in times of summer
drought. Considerable amounts were also used to line the beds
of the newly-built canals; it was laid in slabs, and then impacted
by driving herds of cattle along each stretch.
Before the age when tar mixed with iron slag (a by-product of the
steel and iron industries) was used, roads were repaired with
flints. These were picked off farmers’ fields, often by
children who were paid small amounts for what they gathered.
The flints would then be split by a ‘flintknapper’. Both
knapped (i.e. split) and unknapped flints were also used as
building material in conjunction with bricks or stone, and many
examples can be seen of what became a vernacular style in towns and
villages all over the Chiltern Hills (e.g. Tring Parish
Church).
The local builders of the time well understood the qualities of the
bricks and limes that were burnt at the kilns in the area. For
mortar they used the scrapings from the flint-surfaced roads and the
trimming of the verges; these they called ‘sidings’. During
the winter months the roads were scraped and their verges cut and
the material so obtained was placed in heaps on the grass borders to
be sold by the mile by the local authority.
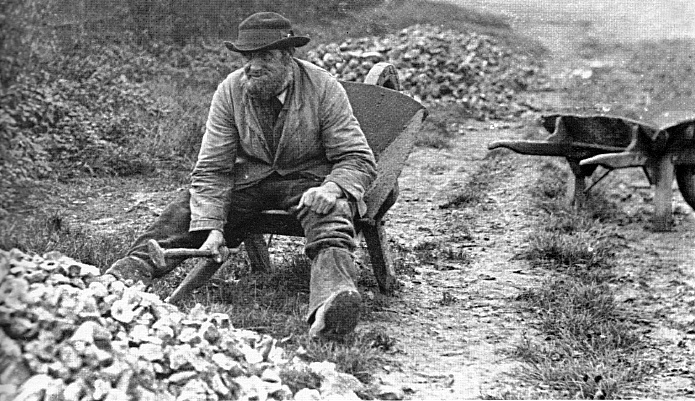
Flintknapping
– Charles Delderfield of Aldbury breaking flints for roadstone
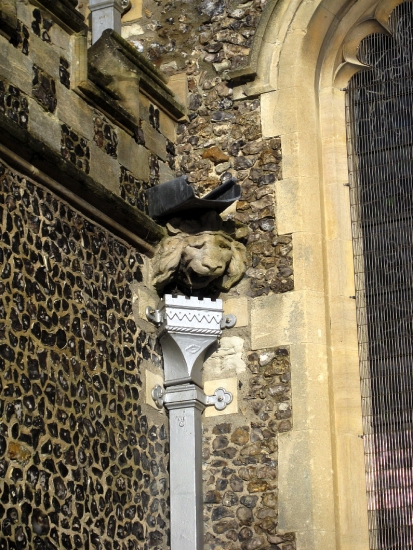
Tring Parish Church
- knapped flint and stone construction
Chapter notes
1. A Hedgehog’s Guide to Northchurch, Bert Hosier, pub.1994.
2. A machine in which clay and water are mixed, blended, or kneaded
into a desired consistency.
3. Charles Smith (1831-1895), a child brickfield worker in the 1840s
who later became a philanthropist and campaigned tirelessly for the
reform of this practice. Eventual success came with the
amendment to the Factories and Workshops Act of 1871 that banned the
employment of boys under ten and girls under sixteen from working in
the production of bricks and tiles.
――――♦――――
4. BRICKMAKING – OUTWOOD KILN, ALDBURY
On the Dairy Farm area of the Ashridge estate before the end of the
16th century, two acres of land known as Lyons Grove were sold and
cleared in preparation for the erection of a brick kiln, but by
about 1723 this brickyard had ceased to function. However,
brickmaking was still carried on in the immediate area, for when one
Daniel Puddefoot, tenant of the farm, died in 1744 his inventory
included “…. For bricks and clay and sand and barrows and all as
belongs to the Brick Trade - £3” (Herts Record Office, 105 HW
12).
Once the 7th Earl of Bridgewater inherited the Ashridge estate in
1803, great changes were in force. An enlightened and
forward-thinking landlord, the Earl brought many improvements to his
properties and land, including plans for a brickworks approached by
a section of new road leading from Tom’s Hill to Northchurch Common.
Known as Outwood Kiln, this enclosure comprised three buildings
forming part of the brickworks, plus a plot containing two cottages
alongside occupied by 1838 by John Howard and Thomas Cox.
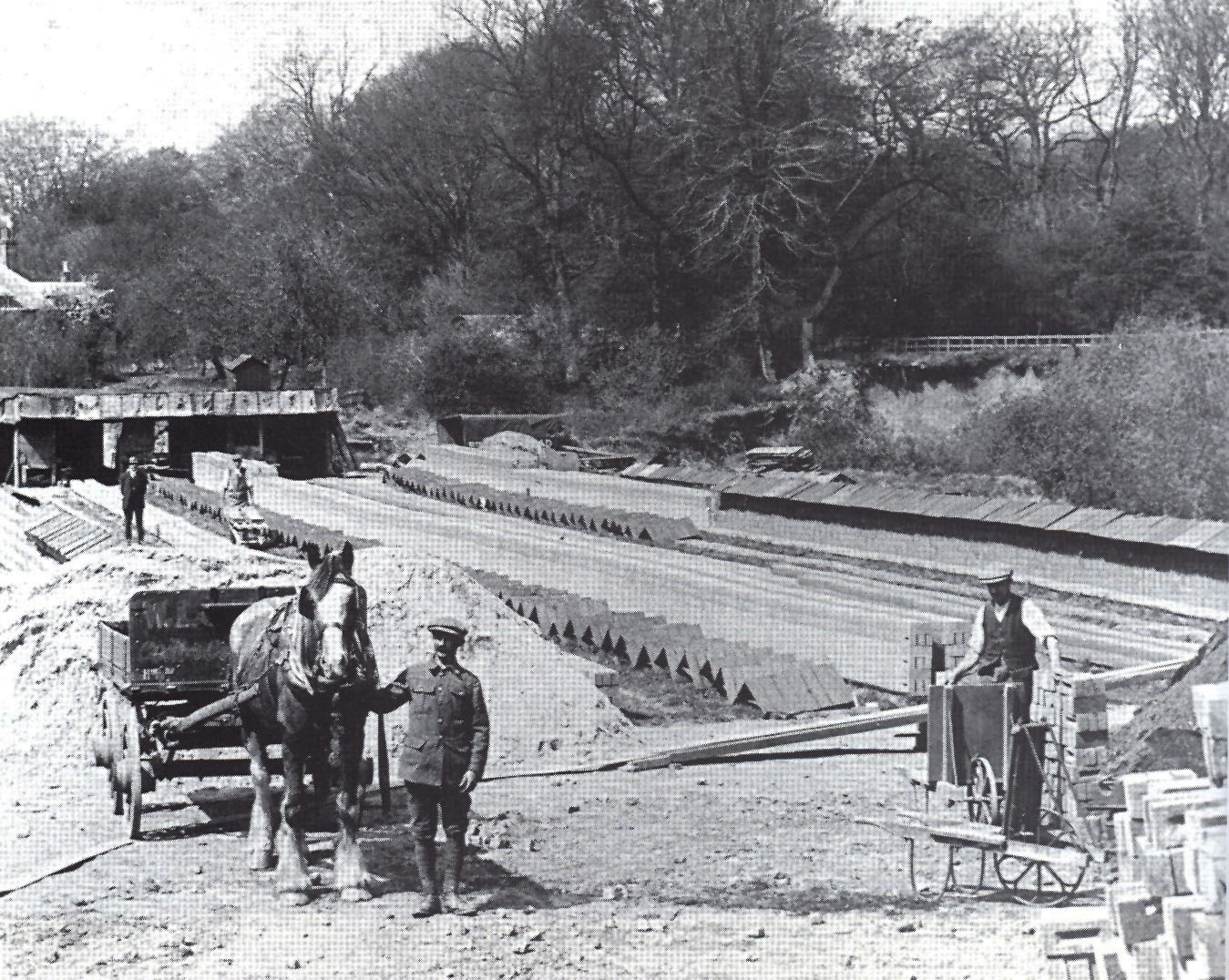
Brickyard at Outwood Kiln,
c.1930s
The exact date when the brickworks became operational can be
reasonably estimated since it was not included on the Ashridge map
of 1821, but cottages described as “at the Brick Kiln on the
common” were being rated by the Vestry four years later.
There appeared to be no protests to the necessary enclosure of five
and a half acres of common land; nor an objection by members of the
Vestry, in fact no recorded disapproving comment of any kind.
It seems likely that it was made clear from the outset that the kiln
would provide work, and that it would produce bricks to build better
homes for the tenants of the estate.
The source of clay for Outwood Kiln would have been the same as, or
similar to, that used by the brick and tile makers at Lyons Kiln as
mentioned above. The bricks, old or new, were a soft pinkish
red in colour and can still be seen in many buildings in Aldbury.
Preparation of clay (‘pugging’) for brick making probably changed
little between the opening of Outwood Kiln and the end of the 19th
century when a horse-gear was in use. The animal walked round
and round, pulling and so turning a horizontal wheel to which was
geared the paddle used to stir the clay.
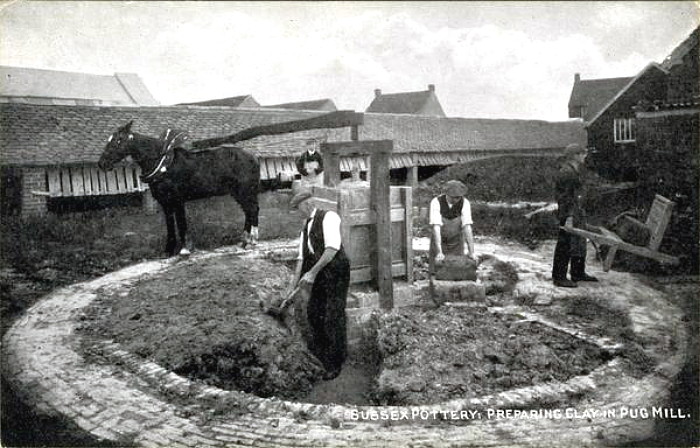
A horse powered pugmill
Clay and chalk, for producing lime, could have been fired together,
as Jean Davis in her Aldbury the Open Village (pub.1987)
gives a description of the process. The kilns were closed by
walling over with lumps of chalk dug nearby; the unfired bricks were
placed above the chalk and a fire was lit in the two kiln pipes.
Large pieces of wood formed the base of the fire, to which were
added small bundles of twigs as well as furze, grass, moss and
bracken, and the fire would burn for three or four days.
Finally, when all had cooled, the bricks were covered with moss and
furze bound together and the kiln entrances were closed.
The bricks were finally removed, and the chalk then slaked with
water, causing it to powder. This was the lime used for mortar
and also to spread and improve the heavy clay agricultural land.
Certainly chalk was burned at Outwood for making slaked lime during
the first thirty years of the 19th century and there is no reason to
suppose methods had changed greatly.
The Outwood Kiln brickworks continued to prosper in a modest way.
Trade Directories of 1878 to 1882 list James Jones as proprietor;
1886 to 1890 Robert Jones; and 1894 Robert Williamson; and an advert
in the Bucks Herald, posted by Albert Ashby, of 6th May 1899
invites applicants for the job of brick-maker.
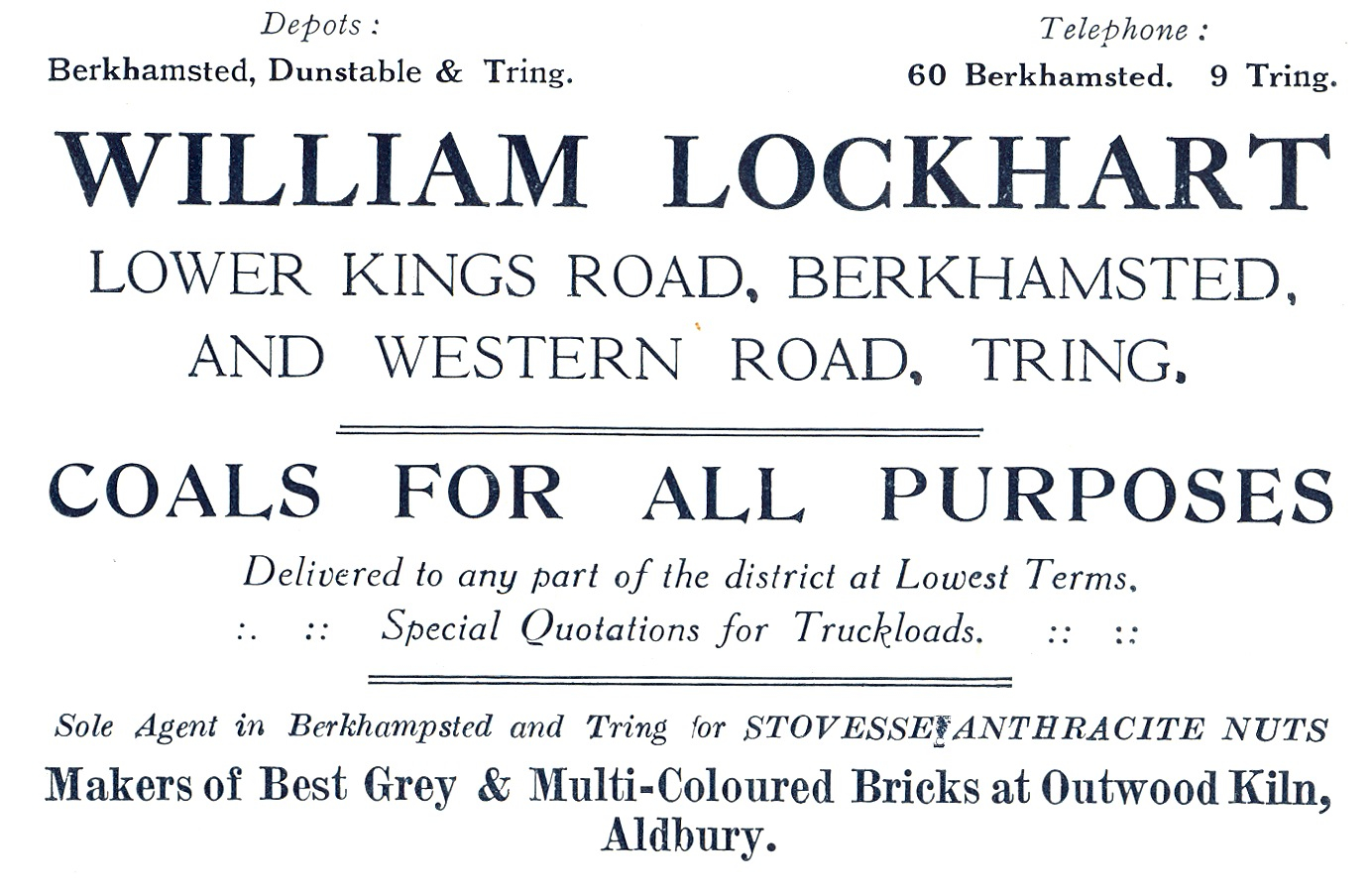
When supplies of suitable clay began to run short, some clay was
then dug at Broomfield Spring (where there are still holes to be
seen) on Northchurch Common, which was then carted to the kiln.
Until the outbreak of war in 1939 when the blackout prohibited the
use of open-topped kilns, the brickyard was operated by Lockharts,
builders and coal merchants of Berkhamsted and Tring. In fact,
many local brickyards had to be ‘blacked out’ for the same reason,
and most did not reopen afterwards.
――――♦――――
5. BRICKMAKING – BUCKLAND COMMON
During the Victorian period, a number of small brickworks were
operating in east Buckinghamshire a few miles from Tring, most at
Buckland Common, where pockets of good clay were to be found.
The records are patchy, ownerships often changed, and the few
accounts can differ in date. But as far as can be discovered,
the first documented brick-maker is Job Brown; [1]
he is mentioned again in matters relating to the Inclosure of
Buckland Common in 1842, and is listed in trade directories in 1854.
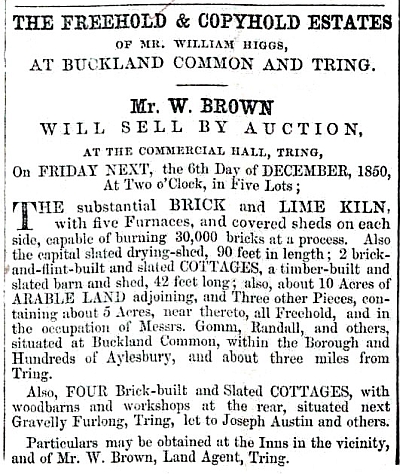 |
Sale
notice for the estate of William Higgs |
When the
Rothschilds acquired the Tring Park estate, a brickworks was already
in situ on a portion of their land holdings on the Common, a yard
that produced hand-made multi-facing bricks in coal-fired Scotch
kilns. [2] The works were managed by George
Gomm of Buckland Wood Farm who appears in trade directories as a
farmer and brick-maker. Slightly nearer to Buckland Wood, a
second brickyard was sited in a field near Twye Cottages. In
1862 George Gomm is offering for sale “at his premises near The
Boot public house, 100,000 prime building bricks. The bricks
are all dry, of uniform size, of splendid colour and first-rate
quality.” The yard finally closed c.1899.
Three members of the Fincher family, John, Charles and Henry, Tring
builders and brick and tile makers, operated from the 1860s to 1961
making ordinary facing bricks and ‘specials’ (brickettes and
water-table bricks for window sills) in three Scotch kilns, also on
the Common at Cholesbury Lane Brickyard (opposite Chiltern
Cottages), using coal carted twice a day from Tring Station to fire
the kilns. As many as 1,000 bricks could be turned out on a
good day, and with work starting at 6 a.m., the brick-maker’s day
was a long one. The heyday of Finchers was the late Victorian
period when an advertisement appeared in the local paper “Wanted,
four good brick-makers. Apply Henry Fincher, Builder, Tring.”
A later advert appeared for a foreman brick-maker “to take
complete charge of brickyard, to dig clay, and make and burn bricks
at per thousand.” The firm constructed many public
buildings and private houses in and around Tring, including the
Church House in 1896, and the schoolroom at the rear of Akeman
Street Chapel, as well as Wigginton Village Hall.
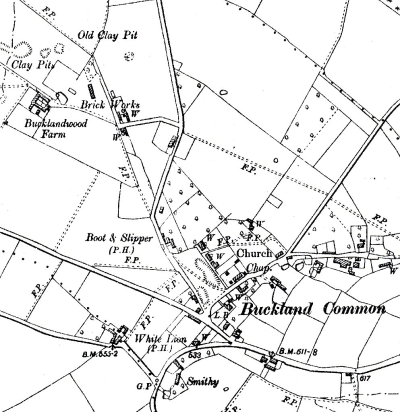 |
OS 1900
showing the brickworks at Buckland Common |
Over the years things did not always run smoothly at this yard.
In February 1909 Henry Fincher prosecuted one of his employees,
Frederick Penn, for the theft of 73 pounds of coal. The police
constable of Cholesbury discovered “black footprints leading from
the yard to the accused’s house, and coal stored in a sack in an
outside shed.”
The foreman at the time, George Dunton, appealed for leniency due to
the accused’s previous good character, and he was fined £1.
Later the firm was run by Henry Cook, and went into liquidation by
order of the Buckinghamshire County Court in 1935, following a
petition brought by Alfred Dunton, an employee who had sustained an
accident at work and been awarded a compensatory payment which had
been discontinued. He claimed that the company was unable to
pay its debts, an opinion with which the judge agreed. [3]
However, the Tring Brick Company did continue trading on the same
site until c.1960s.
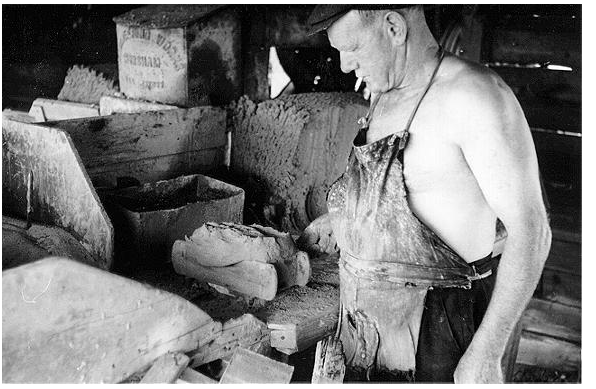
Moulding bricks at
Fincher’s
Brickworks, c.1960s
A short way out of the village, another firm of Tring builders,
Harrowell Brick Co. Ltd., operated in Oak Lane on a site of six to
seven acres. This works traded from c.1923 to c.1949 making
multi-facing bricks also in coal-fired Scotch kilns. During
WWII Fred Harrowell advertised in local papers, offering air raid
shelters constructed of either brick or concrete, suitable for six
to eight persons with construction within seven days, and at a price
of £34 each.
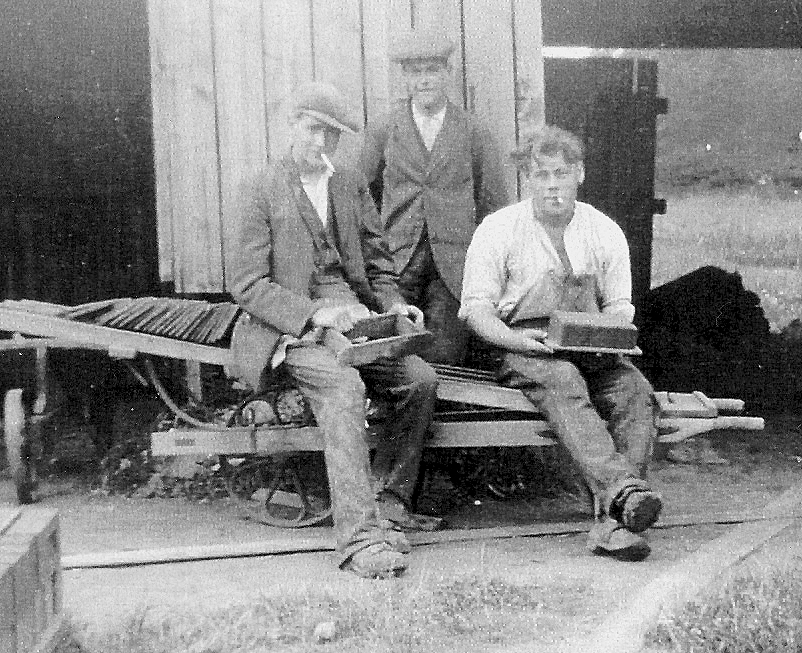
Harrowell’s
brick workers, Oak Lane, c.1930s
William Harrowell had founded the building business in the middle of
the Victorian period and the family also owned a brickworks at a
site in Shootersway, Berkhamsted. Many houses in the town are
constructed using Harrowells’ bricks moulded from the pockets of red
clay found in this area. [4] An anonymous
worker at this yard wrote an account of his hard-working days in the
1930s. [5] He describes digging the clay
from September to May; followed by cleaning out the pugging machines
[6] and the brick making tables, and ensuring
that the hacks [7] and covers were ready.
Four tons of the best coal was usually required for a burn, which
reached white heat towards the end of the firing process; he
commented that manoeuvring a loaded barrow filled with 120 bricks
down the ramp from the kiln took considerable skill, and laments
that the real craft involved in the brick-making process has been
lost due to mechanisation.
Chapter Notes
1. Index of Poll on 31.7.1839 for the Hundred of Aylesbury.
2. Scotch kiln – employing an up-draught which replaced the old
clamp firing method, thought to have been developed during the 17th
century when coal was used instead of wood or peat. Used by
small brickyards, these were open-topped chambers with six to ten
fire holes leading under a perforated floor into which the bricks
were stacked. After filling, the whole was covered with
loose-burnt bricks; firing taking from three to five days, with two
to three days of cooling. Capacity could be up to 80,000
bricks.
3. Bucks Herald archives July-September 1935.
4. The Berkhamsted Review, July 1996
5. Chesham Bricks, Keith Fletcher, pub.2005
6. Often a horse-drawn mill for mixing clay with other materials,
usually with a rotating blade.
7. Drying racks.
――――♦――――
6. BRICKMAKING – CHOLESBURY and HASTOE
Cholesbury - Shire Lane
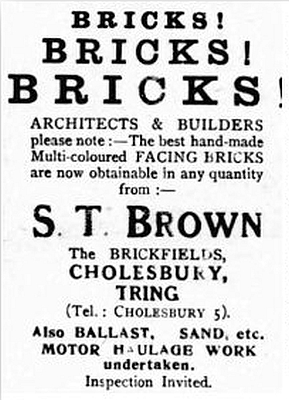 |
Sale of
bricks by Browns |
The demand for
housing after WWI led to the opening of S.T. Brown’s brickworks in
the 1920s on clay fields in Shire Lane. At its height, the
yard was producing 3 to 3.5m. bricks per year in coal-fired, and
later oil-fired, Scotch kilns.
This yard produced a number of different brick types, including
handmade facing bricks, and those known as ‘overburnts’ – meaning as
the name implies, overcooked bricks which are not impaired in
usefulness but making them less desirable commercially. Overburnts,
a large house built of these bricks and situated on Cholesbury
Common, was erected by the proprietor Samuel Thomas Brown (known as
Tom) as his own residence. A well known local figure, he died aged
96 and his obituary appeared in the Bucks Herald on 1st September
1950, describing a versatile man, who during the course of his life
had worked as a publican (licensee of the Rose & Crown, Buckland
Common), a farmer and pheasant breeder as well as a brick-maker. In
addition to his two farms, [1] Tom Brown acquired
a second brickfield at Hog Lane, Ashley Green, and also supplied
ballast, sand, and provided a motor haulage service. In 1938, the
old Buckland Wood Farm site was bought by Browns for its reserves of
clay. This business continued until c.1978 and the area is now
levelled.
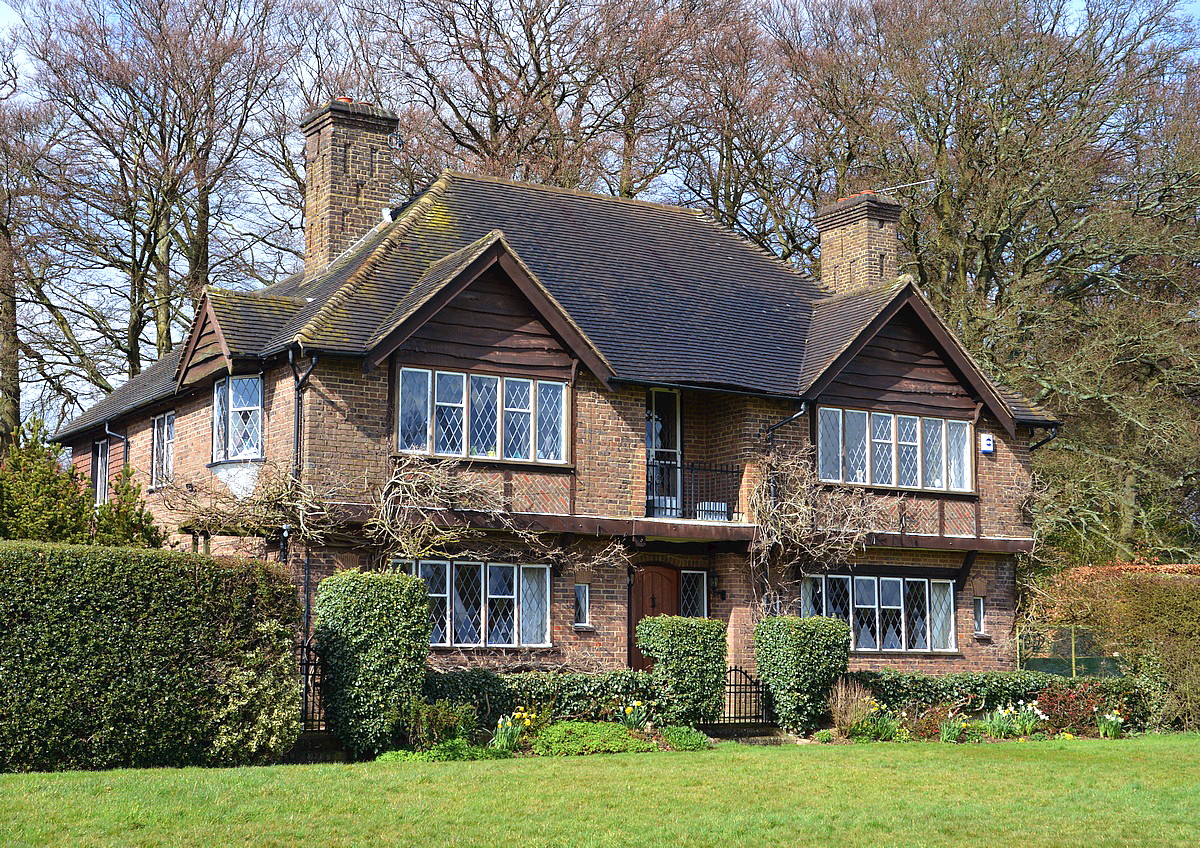
‘Overburnts’
in 2016
Until 1937 six Dunton brothers, their father and three uncles all
worked at H. G. Matthews in Bellingdon. That same year saw the
opening of their own business on a six-acre site almost opposite,
specialising in the manufacture of handmade bricks, clay roof tiles,
gauged arches and fireplace brickettes; due to scarce capital
resources production entailed the use of a very crude kiln. Output
was doubled by 1939 but WWII put an end to further operations.
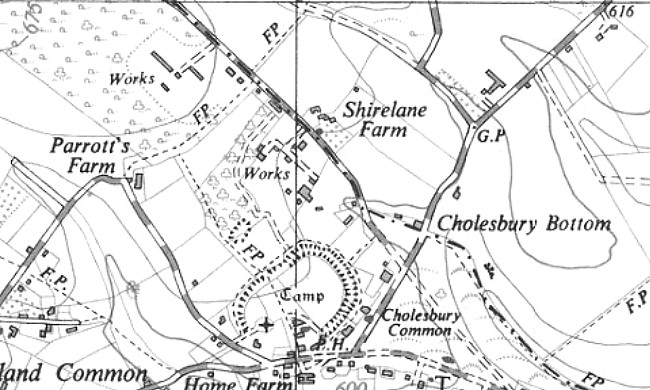
OS 1938 showing Brown’s
and Dunton’s
brickworks
After the war, when the acute shortage of housing created an
enormous demand for bricks, the Ministry of Works encouraged Dunton
Bros. to rent land in Drayton Wood, Shire Lane, on a site adjacent
site to Browns. At a UDC meeting in Tring in June 1946 the problem
was outlined when it was reported that the Ministry would not allow
the town’s proposed new council housing in Park Road to be
constructed using ‘facing’ bricks as specified by the architect, but
that plain flettons would have to do, possibly with a cream-coloured
render. The lack of progress on this Park Road site, due to the
post-war dearth of building materials, prompted the Council to send
a deputation to the Ministry of Works. [2]
Dunton Bros. traded at Shire Lane from 1946 to 1960; two cottages at
Longcroft located at the western end of the lane are built of bricks
from this yard, most traces of which have now gone but the old
workings provide a good home for local badgers.
In 1952 Duntons purchased 68 acres at Meadhams Farm, Ley Hill, for
seasonal brick production in two Scotch kilns. Some clay from here
was also taken to Shire Lane, and by the late 1950s weekly output
was 34,000 per week at Ley Hill and 40,000 at Cholesbury. After
several changes of ownership, and an increase to four kilns, the
firm was acquired by Michelmersh Brick & Tile Company, at that time
employing a high ratio of staff compared with other modern concerns,
as one third of the bricks were still moulded by hand. Due to
difficulties in the construction industry and to bad weather, the
closure of this smallest and oldest site in the group was announced
in 2013, when the area was then scheduled to become a waste dump.
Hastoe – Kiln Lane
A section of a map accompanying the sale particulars of the Tring
Park estate in 1872 marks exactly the site of the brickworks in Kiln
Lane, and an OS map of 1877 (below) confirms the location of clay
pits, kilns and pumps in High Scrubs wood at Hastoe. (Some 50 years
before then, a “brick-ground and cottage at Hastoe Cross, of just
over 15 acres in extent, and a rent of £11.5s.0d. p.a.” was
included in a previous sale of Tring Park estate; this possibly
refers to the same brickfield as that shown on the 1877 map but one
cannot be definite.)
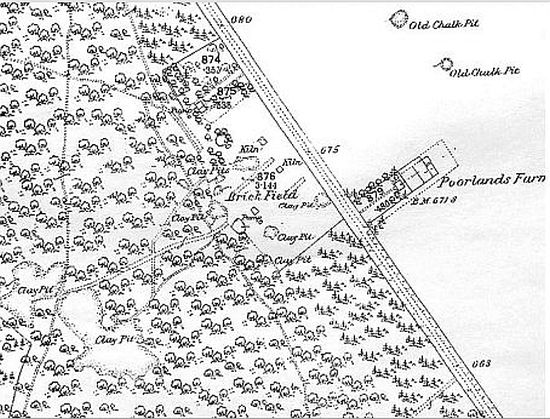
OS 1877 showing brickworks
in Kiln Lane
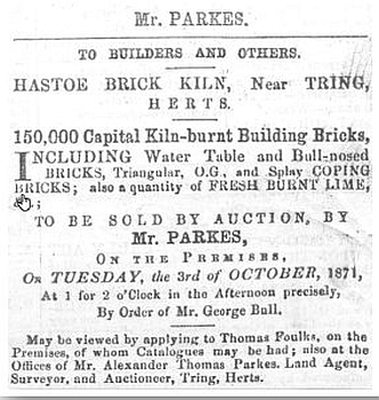 |
Sale of
bricks by Alexander Parkes, Sept 1871 |
George Bull of
Oakengrove Farm in Shire Lane was the proprietor and is listed in
Kelly’s trade directories of 1860 to 1874. But he was operating
before these dates, as the invoice below records that he supplied
bricks to the Rothschild Aston Clinton estate in the late 1850s, at
a time when the mansion house was being enlarged and remodelled and
much building material was required.
Shortly before the acquisition of the Tring Park Estate by the
Rothschilds, sales of bricks from this area were arranged by
auctioneer and agent of the Estate, Alexander Parkes.
When Bull’s kiln closed is again difficult to establish, but as late
as 1891, the census return lists Charles Brown, brick-maker,
residing with his family at Hastoe Kiln. In WWII, local people
recollect pits in High Scrubs wood being filled in using student
labour. This action, reported in the Watford Observer of 1st March
1940, was taken seemingly because of considerable subsidence in the
wood, where trees had actually sunk in to large holes.
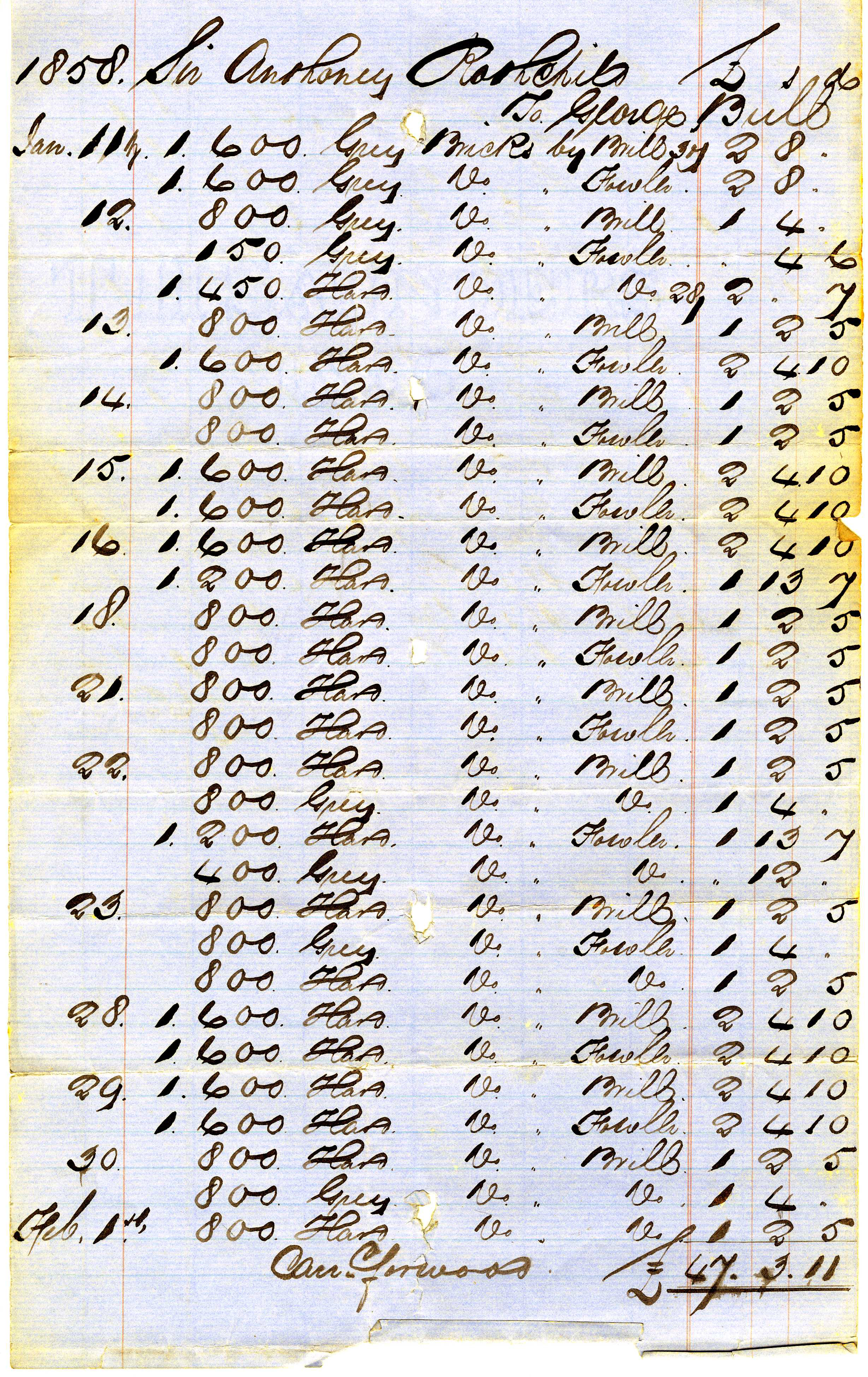
Record of bricks
bought from local suppliers by
Sir Antony de
Rothschild
Chapter
Notes
1. During WWII brickmaking became low priority, so Tom Brown
reverted to farming and acquired the 154-acre Buckland Wood Farm
opposite one of the defunct Buckland Common brickfields. This
farm was sold at auction when the Tring Park estate was broken up.
2. One of these gentlemen was Councillor Harrowell, a Tring builder
and brick-maker (see Buckland Common section).
――――♦――――
7. BRICKMAKING – WIGGINTON
In the Victorian period, members of the Honour family had diverse
business concerns in or near Tring. These included building,
brickmaking, undertaking and horticulture. Their brickmaking
operation was centred in Chesham Road, Wigginton, where clay was dug
from a small pit, which was abandoned when exhausted, and another
then hollowed out. The site and pits are shown on the map
below:
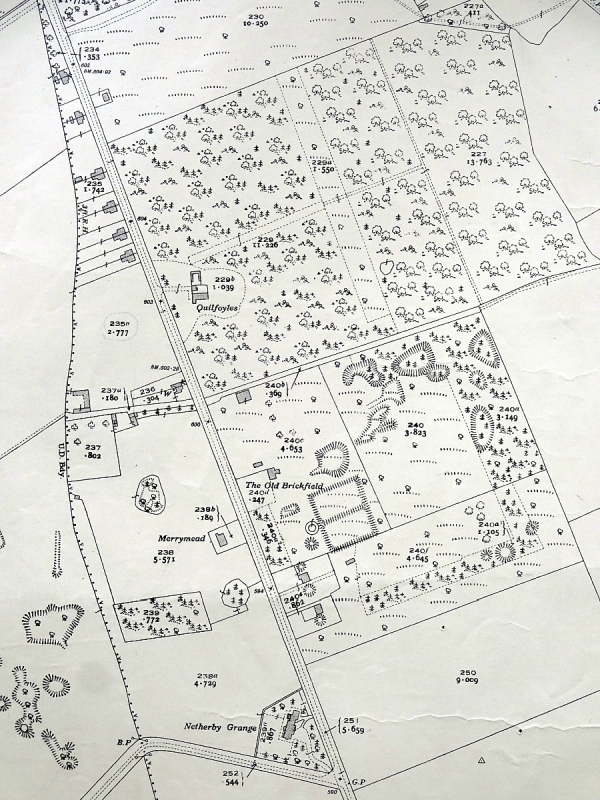
Map showing location of brickyard in Chesham Road
Among many local buildings constructed by Honours and probably using
their own bricks, are two picture palaces, one in Chesham and old
The Empire in Akeman Street, Tring, which is the last of the town’s
three purpose-built cinemas still standing, the premises having been
put to various uses since closure in the 1930s. Honour’s also built
a house in Chesham Road to accommodate their own family, almost
opposite to the brickyard and known as Netherby Grange.
A second and earlier brickworks in this area was owned by Thomas
Little. a well-known local farmer of the 433-acre Tring Grange Farm;
the clay pits and brickyard were situated in Roundhill Wood, on the
Chesham to Cholesbury road. An account in the Bucks Herald of 1840
stated “last Saturday, a notorious character named Joseph Cox,
was committed for two months hard labour for damaging the brick kiln
belonging to Mr Thomas Little of Tring Grange Farm.” Thomas
Little evidently prospered, as eleven years later the census for
Wigginton shows him employing 16 men on the farm, and another nine
in brickmaking.
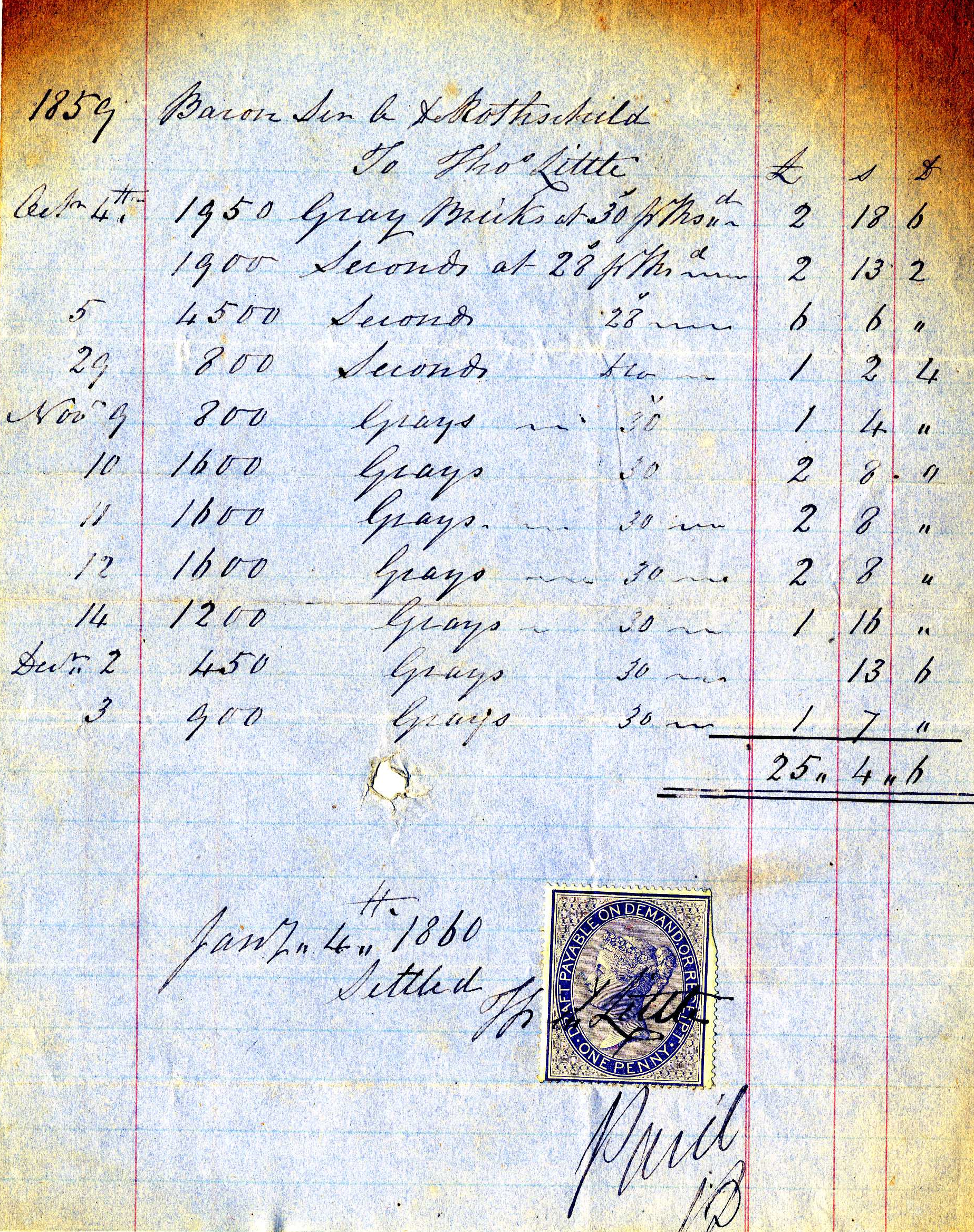
Receipt for
bricks from Thomas Little to
Sir Anthony de Rothschild
Thomas Little appears to have ceased trading in bricks in 1885, when
the stock of bricks, together with all the tools and utensils
connected in manufacture, were offered for sale. After giving up
Tring Grange Farm, Thomas Little retired, took himself off around
the world, and intended to start a well-boring irrigation business
in Queensland which he proposed to name ‘Tring’.[1] But he met a sad
end, possibly due to his very short sightedness, by walking into the
‘death-trap’ near Brisbane [2] and was drowned.
However, two years before Thomas Little ceased farming, James Honour
is listed in the Tring Park Estate account books as renting
‘brick-ground, kiln etc. at Tring Grange’. It is also likely that
James Honour took over the works in Kiln Lane, Hastoe, following the
departure of George Bull c.1878, but just who owned what and when in
the Wigginton area is rather difficult to pin down.

Sale of bricks by Thomas Little, 25th September 1885
Closure of Tring Grange Brickworks
Chapter
Notes
1. From the writings of Tring historian, Arthur Macdonald, c.1890.
2. Storm water drainage systems beneath the city.
――――♦――――
8. OTHER LOCAL BRICKYARDS
Wendover
Never known as a brickmaking area, there is a reference in 1688/9 to
a brick kiln on Birche’s Peece. [1] In the
Militia List of 1798 for the town, Nathaniel Winfield is listed as a
brick-maker, although exactly where he worked is not known.
Aston Clinton
A Rate Book of 1862 lists an area of over two acres comprising
brickyards, kiln, sheds and meadow at Normill Terrace, Aston
Clinton, but no other details. Nearer to Aylesbury another
brickworks owned by the Bonham family is documented; [2]
this operated from c.1864 at Broughton-cum-Bierton on a site now
covered with large ponds. The company, then known as W & G
Bonham, was dissolved in 1887. [3] This may
not have been too disastrous because, like many businessmen in the
Victorian period, George Bonham had many strings to his bow, as he
is described as grocer, baker, brick-maker and post master.
Berkhamsted
That bricks were produced in the Berkhamsted area for probably
hundreds of years is evidenced by the name of ‘Brickhill Green’ at
the top of the town on the south side. A medieval pottery
existed at nearby Potten End [4] where many years
later a brickworks was established. In the early 19th century,
John Hare Nash occupied four acres, comprising a cottage, garden,
woods and a brickyard. How he fired his kilns is something of
mystery, as the Ashridge Steward of the time had forbidden him to
cut furze, the traditional fuel, the reason being so much was
already being taken by owners of kilns at Coldharbour, Aldbury,
Kensworth, and Ivinghoe. Nash may have ignored the ban, or
used wood from his own land; in any case, this operation continued
for almost a hundred years employing four men and three boys.
John Nash’s son expanded the business and increased the workforce by
four men, until he retired and sold his plot to a nurseryman.
A local competitor was Daniel Norris at Little Heath, who advertised
in the local press “bricks of all kinds.” Both yards closed
at the about the same time at the end of the century.
The 1833 London & Birmingham Railway Act had stipulated that the
line was not to deviate from the authorised route when passing
through the grounds of the Norman Castle (probably the first
instance of what we would now call a ‘preservation order’), no
structures, except for necessary bridges, culverts etc., were
to be built, neither was the Company permitted to make bricks or
burn lime anywhere within the parish.
Some 30 years later, on the opposite side of the valley, according
to local historian, the late Percy Birtchnell, “kilns were a
familiar sight on the skyline in 1863”, and these kilns operated
for another hundred years making bricks on the upper part of Bell
Lane and Darrs Lane. According to the particulars of sale for
the Rossway Estate “The freehold property and brick and lime
works with two kilns and drying sheds, plus three cottages, gardens,
barns, stables, cowhouse comprise over 14 acres and are in
occupation of John Skinner.” In 1883 John Howard is listed
in the Pigot’s Directory as a brick-maker at Woodcock Hill,
Northchurch. Brickmaking continued in Shootersway until well
into the next century in a yard operated by Charles Harrowell [see
Buckland Common section].
Ivinghoe
A specialised activity peculiar to the immediate area, was the
short-lived industry of digging for coprolites. [5
and 6] On land in Ivinghoe Parish owned by Earl Brownlow
and rented to Thomas Gale, a seam was discovered in the late 18th
century, and several sites were worked until the late 1870s; where
clay lay beneath the fossil bed, this was sometimes combined with
brickmaking. [7] Another tenant farmer on
the estate, Richard Burdett of Horton, also received licence for
coprolite digging on his fields, and later turned to brickmaking. [8]
The coprolite industry most likely was almost finished by the time
Foxons set up the Ivinghoe and Horton Brick & Tile Company in 1877;
the following year an advertisement appeared in the Bucks Herald
“a Good Sand Stock Brick-maker – apply at Ivinghoe and Horton
Brick Yard.” But no mention is made of the coprolite trade
in a directory six years later when Jasper Foxon is shown as working
as foreman at the brickworks. He is followed after two years
and until 1920 by Thomas Foxon listed as brick-maker in what was a
small yard producing yellow-coloured bricks; these were used in the
construction of several buildings in Ivinghoe village. On OS
maps from 1877 onwards the brickfield is marked on the B488 road as
‘Old Kiln’. The company was dissolved c.1932 [9] and the site
is now occupied by a bungalow.
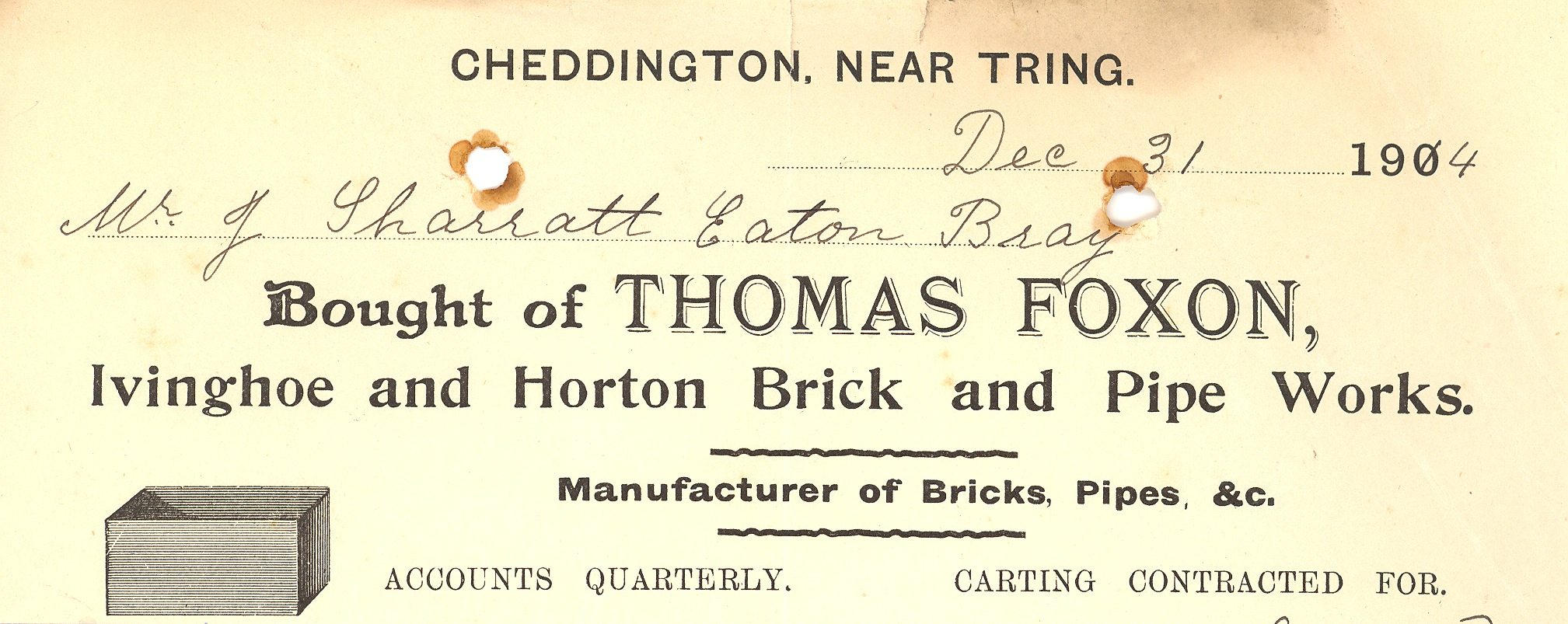
Invoice
heading from Foxons of Ivinghoe
Bellingdon
The only local brickfield still in business but a little outside the
immediate area of Tring is H. G. Matthews founded at Lye Green in
1923; their operation at Bellingdon near Chesham followed shortly
afterwards. At the peak of the industry, 23 brickfields were
operating within a radius of Chesham, but this has now dwindled to
three, mainly due to lack of new deposits of clay, although the firm
of Matthews owns 1,000 acres. A policy of careful restoration
on the site of old workings is always maintained.
The firm continues to produce half a million high-class bricks of
different types each year from clay found in the original deposits
both at Bellingdon and Chalfont St Giles, although clay can now be
dug at greater depths than in the old days. Bricks are moulded
both by hand and by machine, and a tour round the yard gives some
idea of the old ways of brick making and the firing of kilns, two
kilns burning wood which produces a greyish-coloured brick, the
final colour depending upon the firing temperature. Up to
1,000 moulds of different shapes are held in stock, some having been
acquired from the closure of nearby Duntons (see Cholesbury
section).
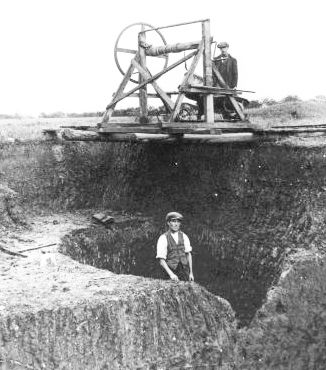
Digging clay by hand
with windlass winch
Matthews’ brickworks, 1924
Matthews’ bricks have been used in several National Trust
properties, as well as at Hampton Court, Chequers, Chesham clock
tower, and Tesco stores at Tring and Amersham. Always known for the
support given to the local community, Matthews donated the materials
to extend Cholesbury Cricket Clubhouse and St Leonards Village Hall.
Marsworth/Cheddington
During the soil excavations necessary during the building of the
Grand Junction Canal, the Resident Engineer, James Barnes, was able
to report [10]:
“In the Summit
at Tring, a part of the canal is executing in the parishes of
Marsworth and Cheddington, where plenty of good clay is found in the
cutting for the purpose of making bricks; my present object for
beginning there was to dig clay this winter ready for making a
sufficient quantity of bricks next summer that will be found
necessary for carrying on the works in this quarter. . . .”
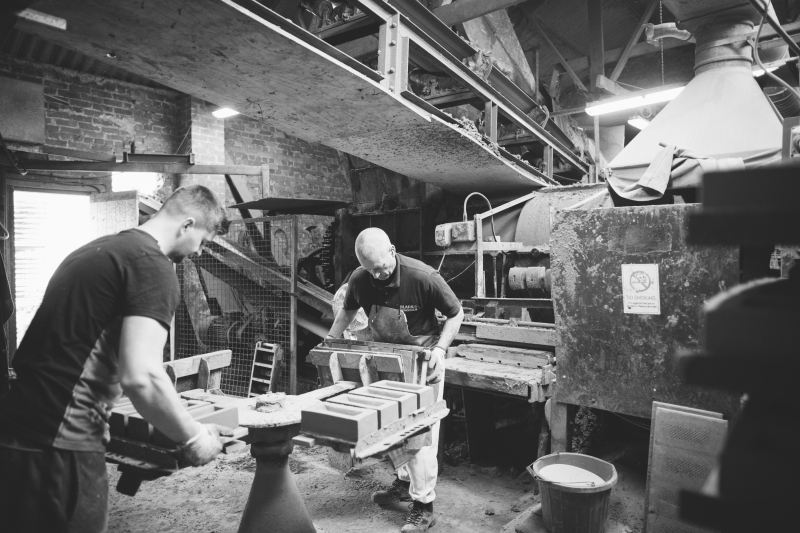
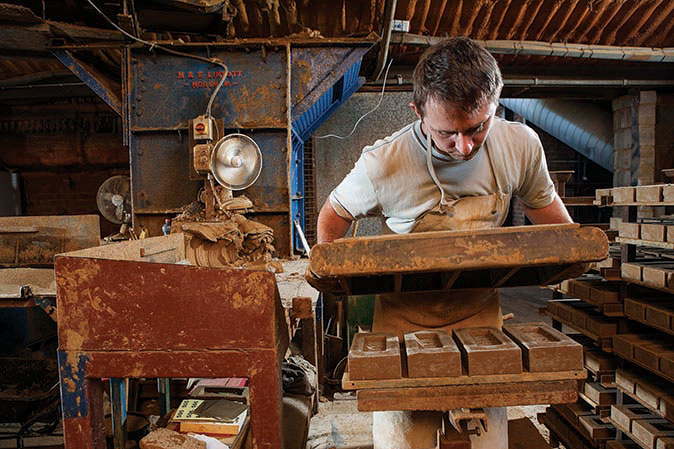
Making bricks
by hand at Matthews, 2016
Six months later, Barnes was again reporting “. . . ..about one
million bricks are made, and nine moulders are constantly employed.
. . .” He then goes on to say that he would put this to
good use by making bricks that were needed for the northern section
of the canal, [11] a measure which would save
considerably on transportation costs; it is reasonable to assume
that these bricks may have been used in the construction of the many
hump-backed bridges leading from Tring to its satellite villages,
but no trace of these canal-side brick-workings has been discovered.
Modern Manufacture
Apart from H. G. Matthews at Bellingdon, none of the brickworks
described in this section survive and workers at those old yards
probably would not recognise today’s methods of manufacture.
Digging and mixing of the clay is highly mechanised, and the early
line and drag machines have generally been replaced by excavators.
Ingredients such as sand, water and anthracite are added
mechanically to the clay before crushing to ensure the right
consistency for easier moulding. Moulded bricks are dried
using gas before being transferred to oil-fired Scotch kilns where
they are fired at higher temperatures for less time than previously.
Chapter
Notes
1. Calendar of Deeds, 1941, Bucks Record Society 5.69.
2. Bucks County Council, ID 0104500000, Monument.
3. Centre for Buckinhamshire Studies, ref. D/HJ/4/1/1.
4. A History of Potten End, Vivienne J M Bryant, pub.1986.
5 and 6. Gazetteer of Buckinghamshire Brickfields, Andrew
Pike, pub.1980:
‘Coprolites’, from the Greek meaning ‘stone’ and ‘dung’, are
fossilised dinosaur droppings, found in the Ivinghoe/Slapton area in
the greensand overlying chalk marl and gault clay. When ground up,
coprolites could be converted into superphosphate for supply to
fertiliser manufacturers.
7. Buckinghamshire Historic Towns Assessment Report, 2012.
8. Kelly’s Directory 1887.
9. National Archives, ref. BT34/179/11256.
10. Report by James Barnes to the General Committee at a meeting on
7th 1797.
11. Marsworth in Living Memory, Carole Fulbrook Hawkins, pub.
c.1997.
――――♦――――
9.
METALWORKING
In Tring throughout the 19th century many craftsmen working with
metal traded in different parts of the town. Not all were using
heavy metal, and their descriptions vary from Iron Founder, Brazier,
Tin-men, Whitesmith, Bell-hanger, Ironmonger, Blacksmith and Farrier.
Sometimes they advertised other specialist craft skills as well,
such as Cooper, Wheelwright and, by 1902, Cycle Agent. Some of the
larger concerns over the years are described below.
G. Grace & Son
The present-day letter heading of G. Grace & Son proclaim that it is
the oldest established family business in Tring, being founded in
Frogmore Street by Sebastian Grace in 1750 (a busy man who married
two wives and sired 18 children). As well as metal working and
ironmongery, at different times members of the Grace family traded
as blacksmiths, whitesmiths, gunsmiths, gasfitters and bell-hangers,
and later pioneered the early motor industry in Tring. In the
mid-19th century Charles Grace located to 29 Akeman Street where he
worked with one apprentice, and then to 34 High Street; it was his
son Gilbert who built the present premises. With its distinctive
wrought-iron balcony, the High Street shop has been a familiar landmark since
built in 1890 to a design by local architect William Huckvale.
The garage workshops behind specializes in
repairing and servicing classic cars.
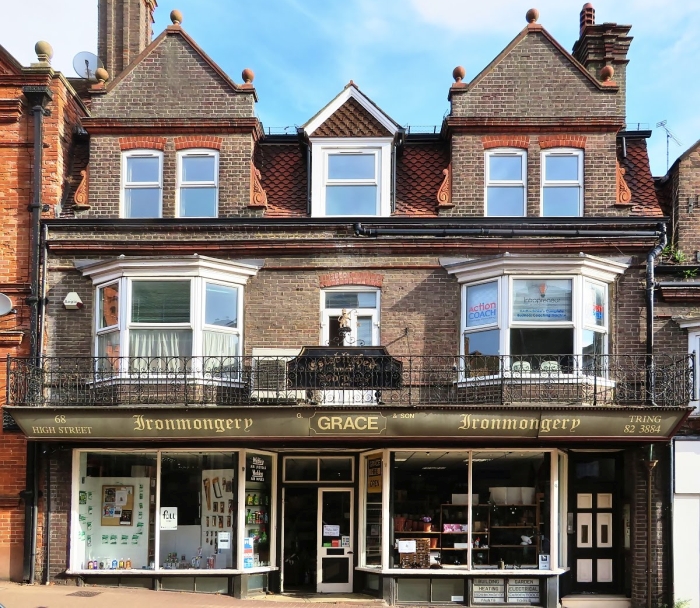
Grace’s
Ironmongery at 68 High Street
At the end of the Victorian period, Graces were advertising as
constructional ironworkers, and examples of their skill can be seen
in different locations around the town. One particular local
curiosity is what is known as the ‘Implement Gate’, made for a
member of the Mead flour-milling family, and for many years sited
opposite the firm’s main entrance in New Mill. The gate has since been
restored and removed to a site in Marsworth.
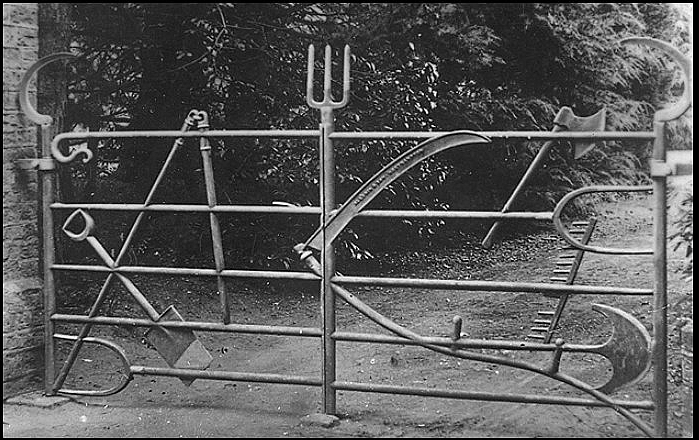
The Implement Gate
Work for the Rothschild family on the private waterworks and central
heating system at Mentmore Towers led to further commissions and to
the supply of materials for their mansion houses both in Aston Clinton
and Tring Park.
Gilbert Grace, the present proprietor of the business and grandson of
the first Gilbert, gives some interesting details of activities at
the firm. The whitesmith plied his craft in what was referred to as
‘the Tin Room’ and this included the re-lining of saucepans and
other types of utensils. The old blacksmith’s shop with its five
forges, situated at the rear of the premises, was burnt out in a
blaze in 1994, thus destroying a reminder of Tring’s heritage. Some
of the metal work manufactured in the forges include the clock face
on the tower of the parish church; and fine large examples can also
been seen in the Zoological Museum in Akeman Street. Before the
Museum was
built c.1889, Walter Rothschild took a trip to Paris accompanied by
Gilbert Grace, who had been commissioned to erect the roof structure.
The purpose of the visit was to gather ideas by viewing the
newly-built Eiffel Tower; the result can be seen by looking high
above the top floor showcases. Other decorative features in the
museum manufactured by Graces include the railings around the
galleries and on the stairways.
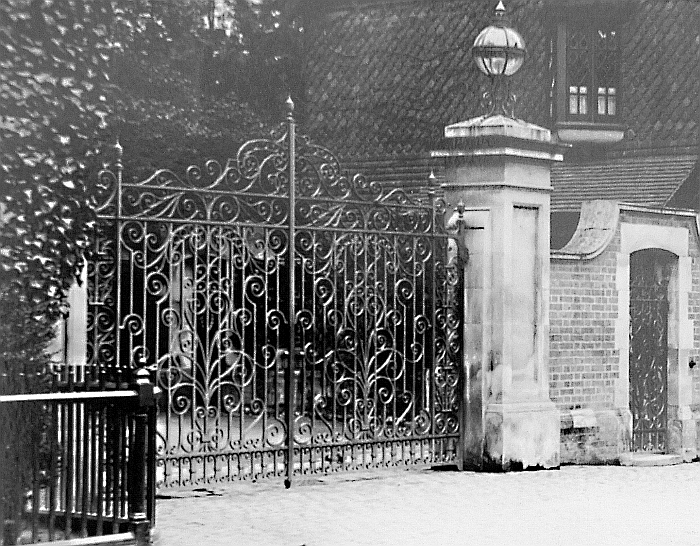
Gates made at
Grace’s premises - entrance drive to Tring Park mansion
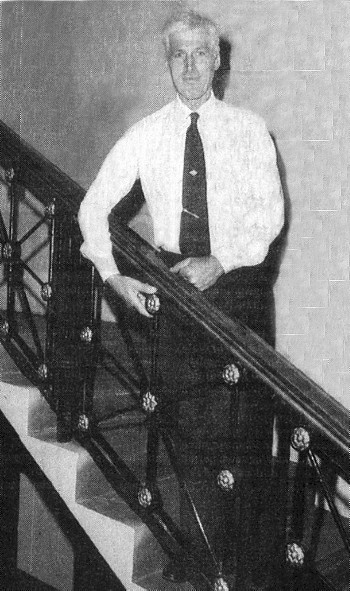 |
Gilbert
Grace on the staircase of the
Zoological Museum, 1992 |
Later, c.1909, a large extension was erected on the east side of the
Museum to house the enormous and growing collection of
insects and to provide more space for bird specimens. The end
result was a group of buildings around three sides of a quadrangle,
the whole presenting a very attractive aspect from Park Street. Graces of Tring again supplied ironwork for the construction of the
roof.
Crawley Bros.
In 1839 William Crawley appears in a Tring trade directory operating in Akeman Street as a wheelwright. By 1850 he
had moved to Western Road on the site of what was the motor
garage of Wright & Wright. In addition to his trade of wheelwright
he also worked as an iron-founder, at that time employing four men and
a boy. Joseph Budd, a Tring local historian, writes that “the
Crawley ironworks was mainly agricultural and industrial
blacksmithing and forging, but not horseshoeing, which was done by
the various farriers scattered about the town.”
Crawley’s premises were sited immediately adjacent to those of
carriage builder George Parrott who had established his business in
1870, and this proximity no doubt proved beneficial to both
businesses.
The third generation of Crawleys, brothers Herbert and Henry,
commenced trading on their own account in Frogmore Street in the
1880s, and then took over their father’s firm three years before his
death. After that, matters did not go well, mainly due to
under-capitalisation followed by the break-up of their partnership.
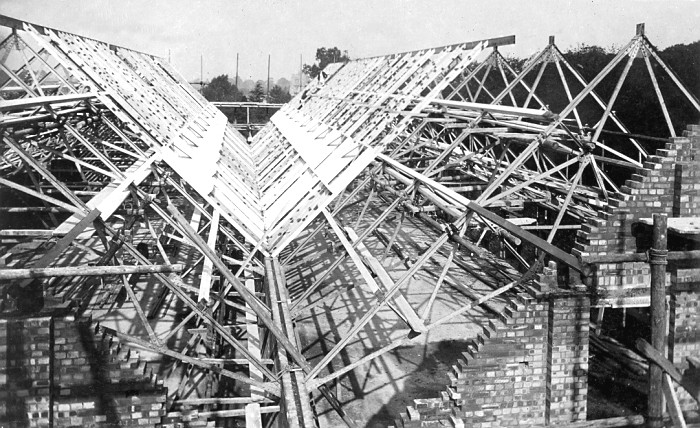
Roof
construction on the extension to Tring Museum, c.1909
Like so many small ventures of this type, craftsmen do not always
make good businessmen and the arrival of the motor car meant a
decline in the trade of the wheelwright. Herbert Crawley ran
the business at a loss until 1900 when he had to admit defeat
with an appearance in the Aylesbury Bankruptcy Court before the Official
Receiver. There he gave a full and candid account of his situation [1]
explaining that he “kept a ledger for debtors, but not a bought
ledger for creditors. He used to keep a slate on which he wrote the
orders, and did not keep any other book except this ledger and the
slate. He never prepared any statement with the object of showing
what his income and expenditure was, neither did he take stock ……”
Unsurprisingly this old-established Tring firm was wound up
and ceased trading shortly afterwards.
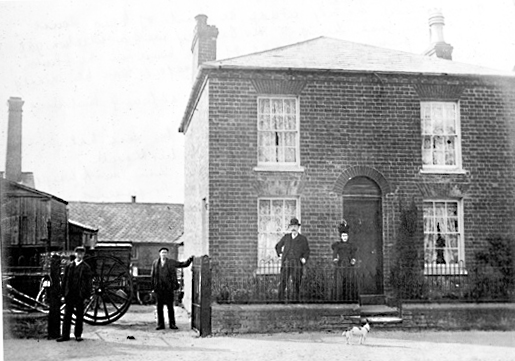
Herbert Crawley outside his house in Western Road
(Parrott’s carriage works on left)
The Crawleys’ neighbour, George Parrott the coachbuilder, retired
and as the garage premises of Wright & Wright were expanding, the
Crawley house was demolished, the outbuildings modernised or
replaced, and the redundant chimney which served the steam-driven
engines also disappeared.
Tring Iron Works
The history of the Hillsdon family in Tring is rather convoluted. John Hillsdon senior was born in Waddesdon in 1805. Twenty years
later he and his wife and five children were living at Gamnel Wharf where
he worked as a miller. By 1850, Tring trade directories list both
John and his son John junior trading as millwrights. In 1861
they are described as ‘agricultural machine makers’, manufacturing
at premises on the corner of Chapel and King Streets in a house and
yard. Today this is a private residence known as
‘The Steam House’.
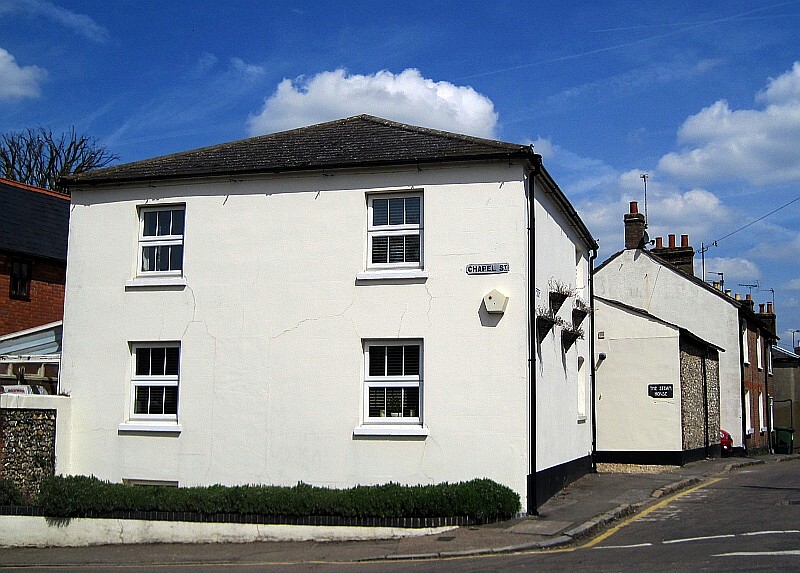
‘The Steam House’ on the
corner of Chapel and King Street
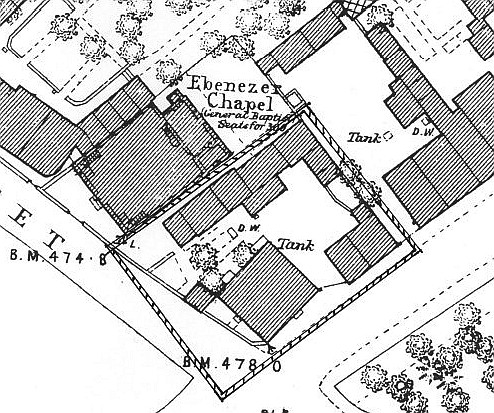
OS 1877 showing
Hillsdons’ premises
At this time their business did not prosper and both were declared
bankrupt in the sum of £587.14s.0d. They were imprisoned for
debt, languishing in the House of Correction and County Gaol in
Hertford.
But their assets were sold to pay the debts and later trading was
resumed. By 1869 John junior was able to display a comprehensive
entry in Kelly’s Directory, being described as an engineer,
millwright, iron and brass founder, manufacturer of portable and
fixed steam engines, water wheels, corn, bone and colour mills. John
junior and his family emigrated to New Zealand but his brother,
George, carried on the business after their father retired and it
is likely that he made the engine installed in the Wendover
windmill. [2] In 1855 [3] the firm erected a new windmill at Quainton.
They also worked on the silk mill in Tring and possibly both the
windmills at Goldfield and Waddesdon, but the best-known surviving
example of their work is sited on Hawridge Common. This tower
mill has recently been (cosmetically) restored with a refurbished cap and
fantail, a new set of sails, and its exterior has been lime-washed
in white. Now a private house with a
colourful past, [4] the present owners have taken care to respect
the mill’s Grade II listing.
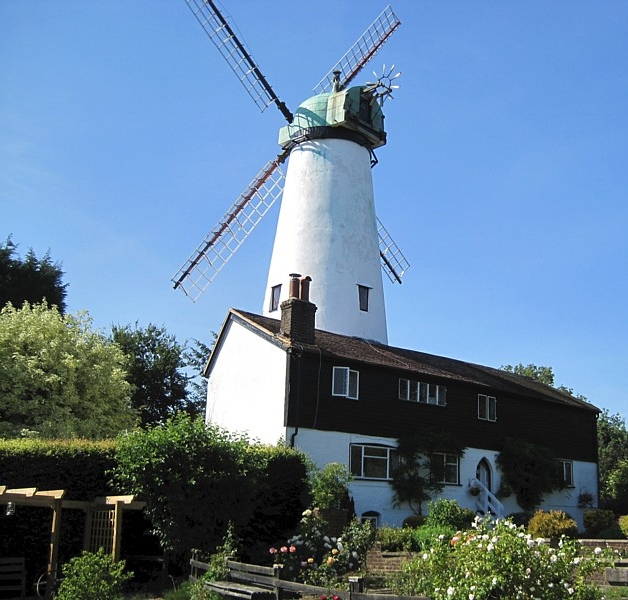
A recent picture of
Hawridge tower mill
A slender tower mill, built in 1883, it was erected by the firm at
what was considered the reasonable price of £300. Replacing the old
smock mill that stood on the same site, some use was made of
existing materials, including ironwork and one pair of sweeps (i.e.
framework for the sails). Hillsdons did not construct the
machinery inside the cap, but probably carried out the installation;
one account states that until a tenant could be found in 1885, being
experiences millers they worked the mill themselves.
After serving the town and surrounding area for 80 years, Tring
Ironworks finally closed down c.1905.
Towards the end of the 19th century a third John Hillson, who may
have been from another branch of the same family, took over the
premises of Charles Grace (see above) at 29 Akeman Street. Shown as
a coach and ironsmith, stationer and fancy warehouseman, it was
not long before he moved to Western Road working simply as a
coach-smith, all mention of ‘iron’ being gone. It is likely that he
was employed in the nearby carriage-building business of George
Parrott, later the motor garage Wright & Wright.
William Tompkins
On the site of the present excellent hardware store of F. W. Metcalfe
& Son, William Tompkins established a business c.1820s, proclaiming
himself an ironmonger and brazier. In those years when
diversification of business interests was common, by 1839 William
and Martha Tompkins were also listed as bakers. This activity
probably arose due to the great influx of labourers (i.e.
navvies) working on the construction of the nearby London &
Birmingham Railway, and Tompkins knew that his shop was the nearest
to the site of their work on the great Tring cutting. He also
supplied the tools necessary for these tough men, as well as
provisions which were referred to by the workers as their ‘tommy’. In the cellar below the present shop, now the area for sales of
kitchen equipment, are well-preserved heavy oven doors set into the
brickwork; the fire beneath vented under the ground emerging outside
the shop frontage, and one wonders what better way to tempt passing
customers into the premises than the aroma of freshly baking bread.
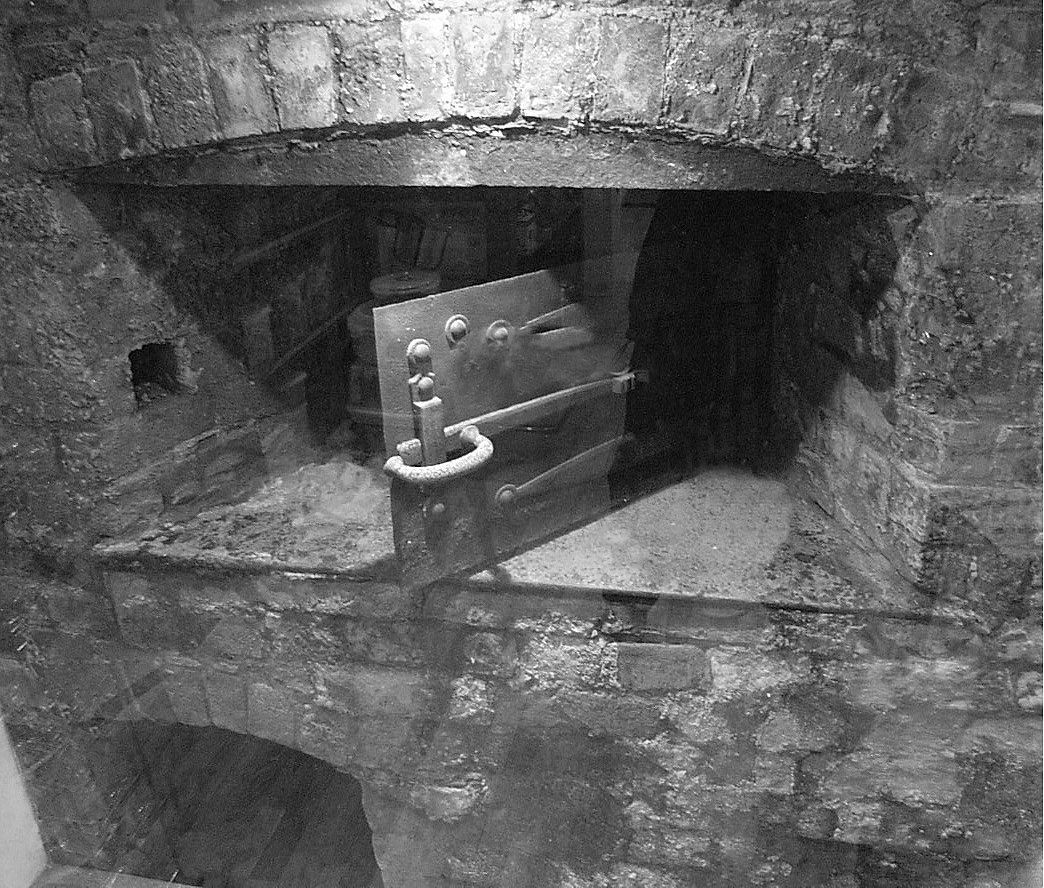
Bread oven in
the basement of Metcalfe’s hardware store, 2016
Two more generations of Tompkins carried on trading, firstly Mrs
Mary Tompkins & Sons who advertised as wholesale and retail
ironmongers, as well as coppersmiths, braziers, tin, iron and zinc
plate workers; stove-grates and ranges were also manufactured on the
premises. One son Thomas took over, and when he died in 1894 his
business was acquired by William and Arthur Dawe, who also had works
in Akeman Street; these brothers moved with the times as among their
varied activities they advertised as cycle agents.
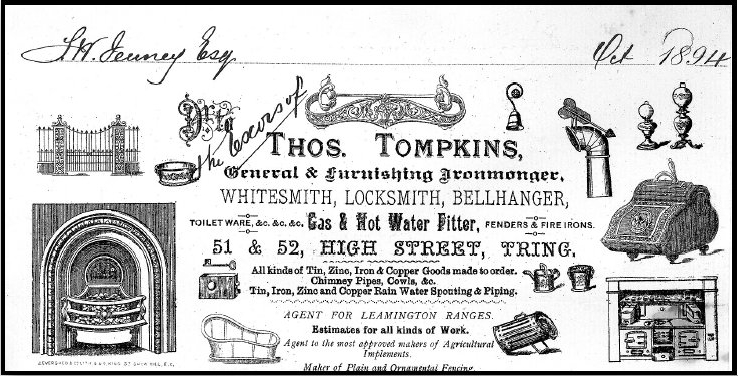
Thomas Tompkins
invoice heading (now Metcalf’s
hardware store)
After a period serving as a motor garage and, in WWII, a Royal Navy
land-ship where barrage balloons and kites were constructed, the
premises once again in 1948 reverted to its original use, that of
retail hardware, a business that three generations of the Metcalfe
family have run since.
Hampshire & Oakley Ltd.
After World War II, Rotherham man H. C. Hampshire, tired of the grime
and smoke, was seeking to escape to the country, but England was
still recovering from five years of upheaval and suitable premises
were hard to find. After a two-year search, an opportunity arose to
acquire the disused Ebenezer Chapel at the top of Chapel Street,
Tring, (Incidentally, this building was immediately next to the old
Tring Ironworks).
Wishing to expand, their hobby of ornamental ironwork developed into
a sound business concern. The firm grew and was soon producing many
types of iron and steel items from wrought-iron gates, lamp
standards, trolleys, and even the framework for a Dutch barn. When
Hampshire died in 1954, Thomas Moy, one of his employees known as
‘Tom the Blacksmith’, took over as leading hand. He made the altar
rails for St Martha’s church immediately opposite the premises, and
the arch over the gates of Tring Memorial Gardens. He left Hampshire
& Oakley in 1962 to become the blacksmith at the Tunnel Cement Works
at Pitstone and, in addition to his normal work, he fashioned the
iron fittings for the restoration of Pitstone Windmill.
Wishing to return to the original trade of his Sheffield days of
spring-making, also led Hampshire to a decision to acquire a
300-year old forge in Akeman Street [below],
for the manufacture and repair of leaf springs for cars and lorries. A modern gas furnace was installed to produce the intense heat
required for the silicomanganese steel needed in the process, but a
few of the old fitments were retained as a reminder of the functions
carried out by those who had wrought iron and shod horses. [5]
After the closure of Hampshire & Oakley in 1970, the old chapel was
used by a company carrying out plastic injection moulding, but is
now demolished and a modern house occupies the site.
Tring Forge
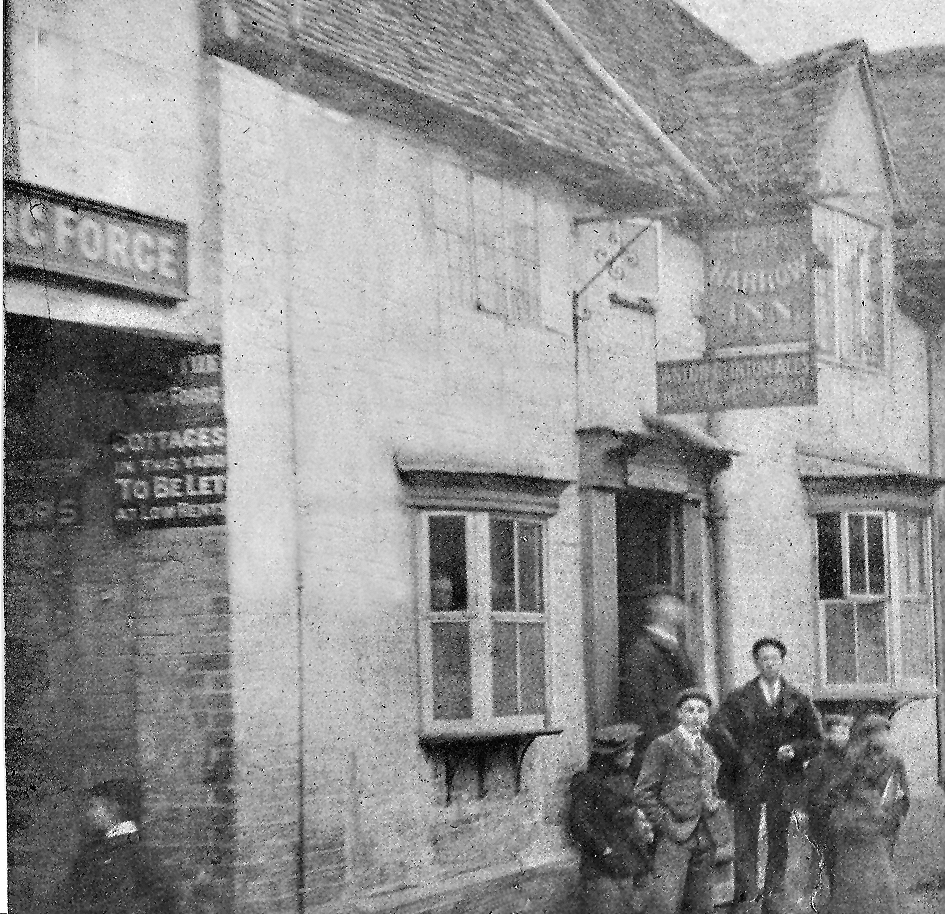 |
Entrance
to Harrow yard and
Tring Forge, c.1890 |
From medieval times or earlier a market town like Tring must have
had blacksmiths and farriers plying these essential trades, but the
earliest mention is not until c.1820 when trade directories list
three individuals, as well as one each in Wigginton, Aldbury and
Wilstone.
The particulars of an auction sale in 1863 of The Harrow pub in
Akeman Street show a blacksmith’s forge in the yard, and this is
marked as a large smithy on OS map dated 1877. These premises were
most likely those used by Hampshire, and over the preceding years
were worked by various proprietors – including at the turn of the
century, Daniel Lines, and before WWII by Frederick Cooper.
This old forge and the other premises in the stable yard of The
Harrow pub were finally demolished in 2006 to make way for new
houses.
Forge at the Bulbourne Works
An attractive Grade II listed group of buildings stands on the Grand
Union Canal at Bulbourne Tring, near the junction with the Wendover
Arm. At first the site was simply a maintenance yard but in 1847 it
was decided that it would be less expensive if lock gates were built
near where they were needed. At Bulbourne a workshop was set up in
the open air, and in 1903 the present buildings were erected. Originally a team of blacksmiths manufactured all the mechanical
parts for the gates, but as time went on modern machinery enabled
the process to be carried out more quickly, and the forge was used
only occasionally.
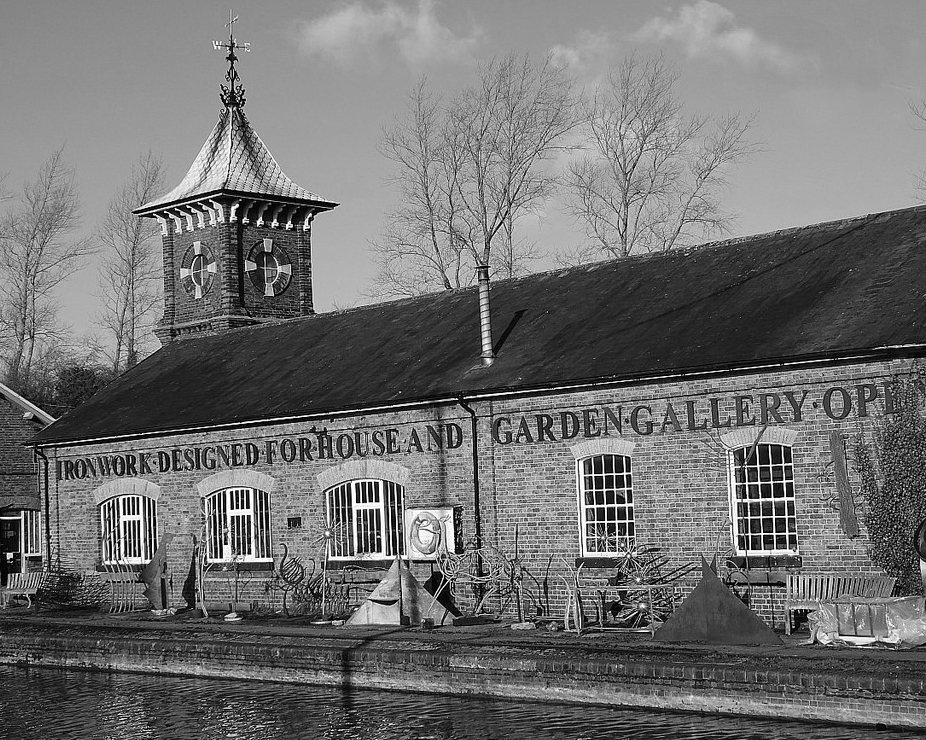
The premises of
‘Hammer & Tongs’, 2015.
The site has since been redeveloped as residential accommodation
However, with the closure of the Bulbourne Works in 2004, the forge
area then again was worked in a traditional way, as Hammer & Tongs,
established in 1988 by master blacksmith Paul Elliott, supported a
group of blacksmith artists using traditional skills to work on
commissions of any size for architects, local authorities and
individuals. As well as items such as railings, balconies and gates,
artwork was produced in both wrought and cast iron, including garden
furniture and water features. Some of the pieces were displayed
outside the old premises, and made an attractive waterside feature
when viewed from the canal or opposite towpath. At the time of
writing, there are plans to develop the Bulbourne workshops site,
including the Grade II listed buildings, for housing.
The Tring Park Stud
Always interested in agricultural matters, and anxious to improve
the stock on both his tenant and local farms, Lord Rothschild set up
a Stud Farm in Duckmore Lane,
Tring, where working Shire horses were bred, stabled and cared for. Among the various new outbuildings set around the large cobbled yard
was a blacksmith’s shop equipped with the whole range of necessary
tools, a soft wooden floor for horses to stand on whilst being shod,
and a manger to keep them preoccupied. Adjoining the forge were a
tool storage area and an engine house with brick chimney.
A blacksmith from Lancashshire, Albert Christopher, was employed as
shoe smith, and it was generally acknowledged among the local
farming fraternity that Bert, as he was known, had a special ‘knack’
with horses. It was claimed that many would only be shod by him, and
in fact he travelled round the area, as well as much further afield
on occasions, to attend to some animals that had been bred at the
Stud. [6]
Following the death of Lord Rothschild in 1915, the whole enterprise
came to an end when the horses were sold and the buildings put to
other uses. But the blacksmith’s shop remains, now serving as a
workshop and base for a mobile forge used by a farrier travelling to
local farms and other locations.
Dancers End Waterworks
Erected in 1866, this attractive industrial building was designed by
George Devey, a well-known architect of the time. Sited at Dancer’s
End on The Crong, a steep wooded hill covered in beech trees, it
occupies a somewhat secluded spot.
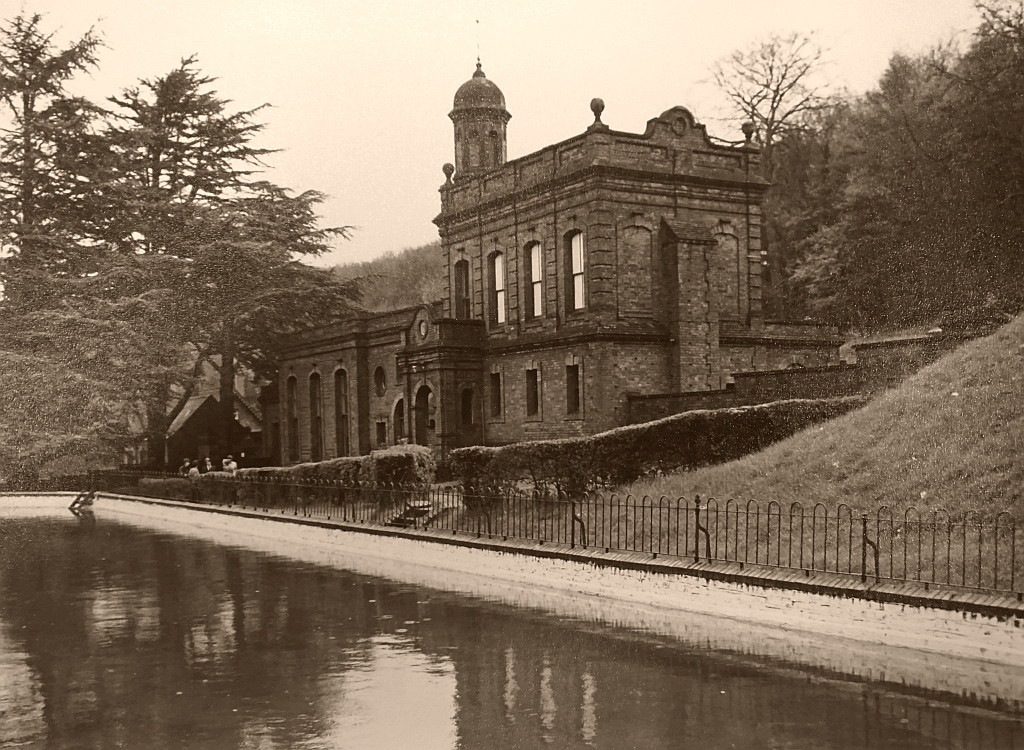
Dancers End
Waterworks
Providing water from the Chiltern
Hills to Aylesbury, Tring and local villages, the main building is
surrounded by ancillary workshops and storage areas. One of these
contains the forge where all the metalwork required inside the main
building was manufactured, as well as the railings enclosing the
various reservoirs. Now used as a meetings room, some of the
original features and equipment remain and are well preserved,
including a black ‘pot-bellied’ stove, and the forge itself, to left
of which is a huge pair of bellows set up high and operated by
pulling on a chain.
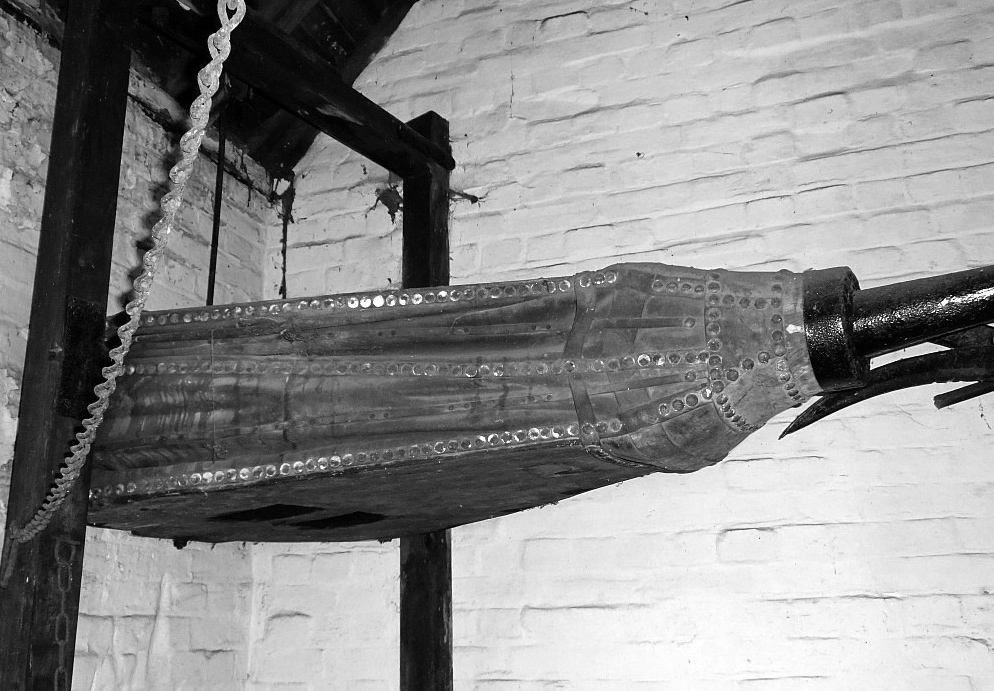
Bellows at
the Dancers End Waterworks forge, 2016
Thomas Goodson & Son
The last reminder of the craft of the blacksmith in Tring is the
name The Old Forge, an attractive property adjoining the main
car-park at the bottom of the town. In this area stood the premises
of Thomas Goodson and his son, members of an old-established family
of farriers at Wilstone. The use of this forge was convenient for
the grooms and coachmen employed at the stables at Tring Park. The
animals shod here at that time included those owned by the
Rothschild family; as well as hunters and carriage horses, zebras,
owned by Walter Rothschild and trained to harness, also required
careful attention to the care of their feet which had to be trimmed
and filed. Although ‘tamed’ to a certain degree, these creatures
remained wild animals and had to be treated with great caution.
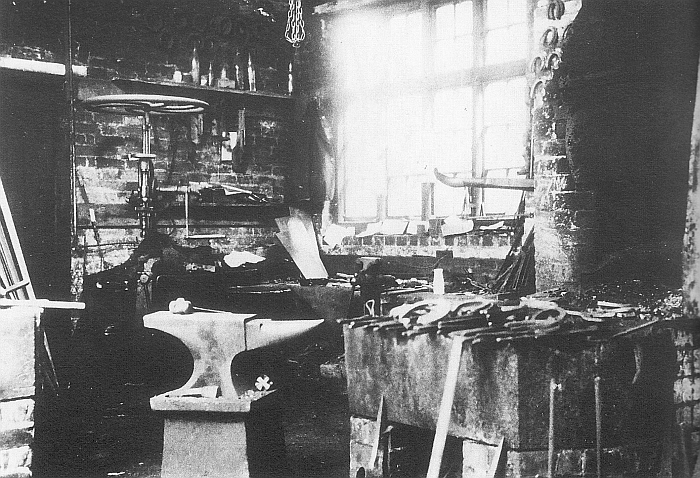
The blacksmith’s
forge at No. 51 High Street where Thomas Goodson
and his son
were blacksmiths.
Jim Goodson retired at the age of 80 and the business passed to
George Stratford with Arthur Gutteridge, who had been taken on as an
apprentice to Jim Goodson, running the forge. These were the years
of the Great War and trade boomed when hundreds of soldiers were
billeted in Tring. He recounted that sometimes he made 200 shoes a
week, and recalled that he remembered horses by their feet rather
than any other part of them; the most perfect feet he ever
encountered were those of a mare named Kerry Clanish Maid, and he
kept one of her shoes for 40 years. [7] Arthur Gutteridge shod
horses until 1940 when he went to a munitions factory, work which
bored him greatly.
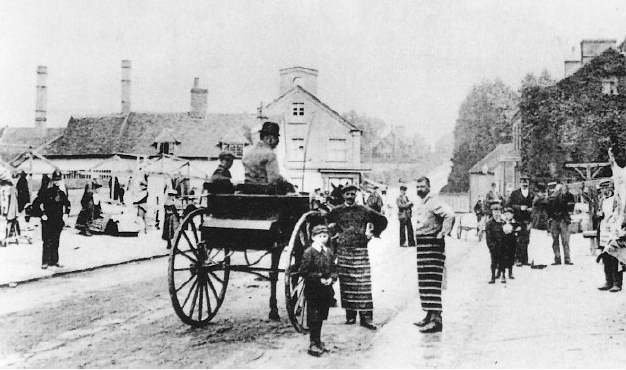
Exterior (showing chimneys) of Goodson’s forge, c.1900
This forge was later taken over by Eric Reed, whose son, as a small
boy, remembers with affection his visits to the premises. After
school, he would brew a cup of tea for his father using an ancient
blackened kettle; then he was expected to pump the fire using
bellows which were operated by pulling on a cow horn attached to a
long wooden arm. Seemingly most of the horses were well-behaved,
probably long accustomed to the procedure and, as Reed sat on a
small stool with his back turned, would obediently lift a foot when
tapped on the leg. But a farrier still had always to remain alert as
all horses, especially the heavy breeds, could suddenly snatch a
foot away, shooting the blacksmith straight out of the door. Unlike
some farriers, Eric did not have a mobile forge, but on Saturdays
would visit outlying farms and stables, having used the anvil to
shape the shoes beforehand. [8]

Tring blacksmith
Eric Reed with a heavy horse in the High Street forge
In 1937 Mrs Stratford is shown as proprietor. After conversation for
use as a doctor’s surgery, the Old Forge is now a private house.
James Elliott DipWCF
The skills of the blacksmith will always be needed and James
Elliott, an award winning UK farrier, today offers a shoeing service
in the Home Counties within a radius of his base at Shire Lane,
Cholesbury near Tring. He advertises a full range of farrier
services including remedial and therapeutic shoeing and barefoot
trim and trimming; all types of horse can be fitted with his
handmade shoes, produced from his mobile forge.
Like his brother James, Charles Elliott was educated at Tring School
and has since followed a career in metalworking. A creative
sculptor, his pieces are in demand by a range of corporate and
private clients, and examples can be seen locally. Married to
international show jumper, Abbe Elliott, his work often reflects her
equine interests, and is constructed using both traditional
blacksmithing and modern metal manipulating techniques.
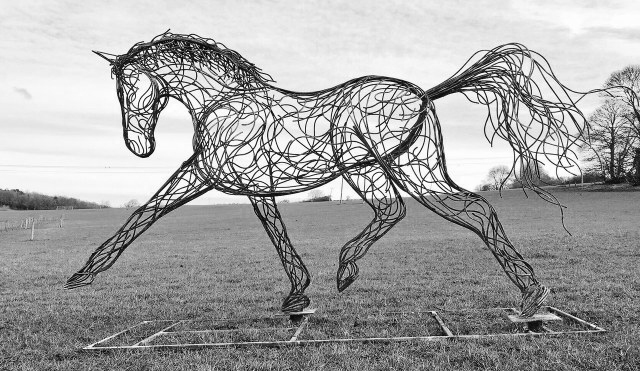
Horse sculpture by Charles Elliott
CHAPTER
NOTES
1. Bucks Herald 10th November 1900.
2. From Book of Wendover - letter of 1932 to Basil Pursell.
3. Bucks Herald 10th November 1855.
4. See
Gone with the Wind: Windmills and those around Tring
by Ian Petticrew and Wendy Austin, pub. 2010.
5. The Changing Face of a Forge, P. J. Young, Hertfordshire
Countryside, Spring 1950.
6. From an article in Horse & Driving, Keith Chivers, 1981.
7. From The Shire Horse, Keith Chivers, 1976.
8. A Memory of my Boyhood in Tring, Don Reed, Tring LHS
Newsletter No.50, September 2005.
――――♦――――
|